Dynamic Modeling Method of Rotating Cylindrical Shell-Variable Section Disc-Pretwisted Blade System
A dynamic modeling, blade system technology, applied in the direction of instrument, geometric CAD, design optimization/simulation, etc., can solve the problem that the radius of the rotating cylindrical shell is smaller than the radius of the disk, and does not conform to the application structure of the coupling system of the rotating cylindrical shell and the disk, etc. question
- Summary
- Abstract
- Description
- Claims
- Application Information
AI Technical Summary
Problems solved by technology
Method used
Image
Examples
Embodiment Construction
[0121] In order to better explain the present invention and facilitate understanding, the present invention will be described in detail below through specific embodiments in conjunction with the accompanying drawings.
[0122] Such as figure 1 and 2 As shown, an embodiment of the present invention provides a dynamic modeling method for a rotating cylindrical shell-variable cross-section disc-pre-twisted blade coupling system, including the following steps:
[0123] Step 1: Construct the three-dimensional coordinate system required for dynamic modeling of the rotating cylindrical shell-variable cross-section disc-pre-twisted blade coupling system;
[0124] The three-dimensional coordinate system includes: the fixed coordinate system OXYZ of the entire coupling system, the coordinate system ox of the variable-section disk d the y d z d , the moving coordinate system ox of the whole system during the motion process r the y r z r , the local coordinate system ox of the pre-...
PUM
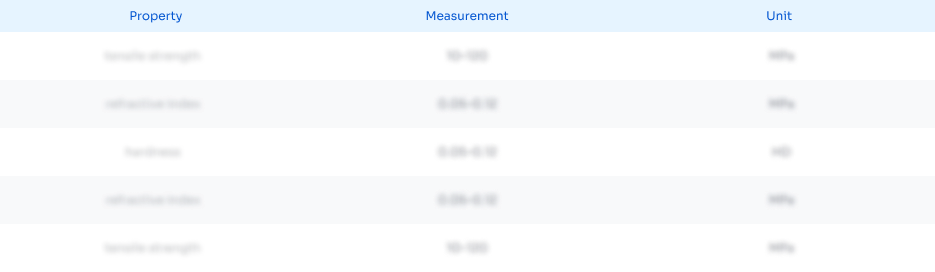
Abstract
Description
Claims
Application Information

- Generate Ideas
- Intellectual Property
- Life Sciences
- Materials
- Tech Scout
- Unparalleled Data Quality
- Higher Quality Content
- 60% Fewer Hallucinations
Browse by: Latest US Patents, China's latest patents, Technical Efficacy Thesaurus, Application Domain, Technology Topic, Popular Technical Reports.
© 2025 PatSnap. All rights reserved.Legal|Privacy policy|Modern Slavery Act Transparency Statement|Sitemap|About US| Contact US: help@patsnap.com