Three-phase PWM rectifier control method and system based on virtual synchronous machine
A technology of virtual synchronous machine and control method, which is applied in the direction of output power conversion device, conversion of AC power input to DC power output, electrical components, etc., and can solve problems such as incompetence in voltage support
- Summary
- Abstract
- Description
- Claims
- Application Information
AI Technical Summary
Problems solved by technology
Method used
Image
Examples
Embodiment 1
[0088] Such as figure 2 As shown, the direct power control method of the three-phase PWM rectifier based on the virtual synchronous machine includes the following contents:
[0089] For any moment, the active loop part adopts PI controller, which can realize the reference active power P ref There is no static difference following, the difference ΔP between the reference active power and the system output active power P is used as the input of the PI controller, and the output of the PI controller is the mechanical torque T m , and its specific calculation formula is:
[0090] T m = K p (P ref -P)+K i ∫(P ref -P)dt;
[0091] Among them, P ref is the reference active power, K p is the proportional coefficient of the PI controller, K i is the integral coefficient of the PI controller. The system output active power P is calculated by substituting the current power grid operating parameters obtained in real time into formula (5). The reference active power P ref Set t...
Embodiment 2
[0113] Such as image 3 As shown, the difference between this embodiment and Embodiment 1 is that in this embodiment, the control mode is DC constant voltage control, the active loop is a voltage loop, and the obtained current DC side output voltage V O and the reference DC voltage to calculate the excitation flux linkage. The specific process is: the DC side output voltage is obtained by sampling the DC side voltage; The calculation formula is:
[0114] T m = K p (V ref -V O )+K i ∫(V ref -V O )dt;
[0115] Among them, V ref is the reference DC voltage, V O is the output voltage of the DC side.
[0116] Based on the same inventive concept as the above method, the present invention also provides a three-phase PWM rectifier control system based on a virtual synchronous machine, including: a sampling module, a mechanical torque calculation module, an excitation flux linkage calculation module, and an AC power grid angular speed calculation module, an AC power grid an...
PUM
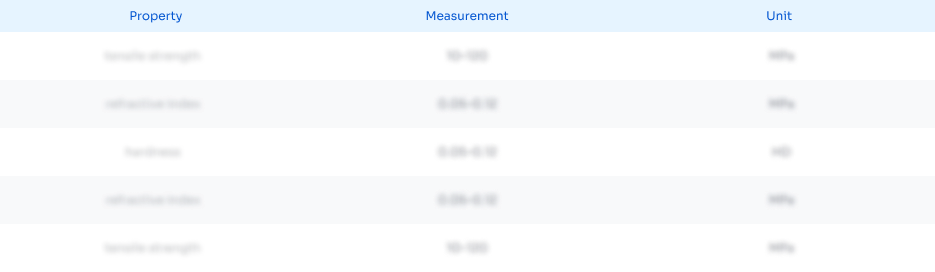
Abstract
Description
Claims
Application Information

- R&D
- Intellectual Property
- Life Sciences
- Materials
- Tech Scout
- Unparalleled Data Quality
- Higher Quality Content
- 60% Fewer Hallucinations
Browse by: Latest US Patents, China's latest patents, Technical Efficacy Thesaurus, Application Domain, Technology Topic, Popular Technical Reports.
© 2025 PatSnap. All rights reserved.Legal|Privacy policy|Modern Slavery Act Transparency Statement|Sitemap|About US| Contact US: help@patsnap.com