Zero-gravity control method free from moment sensing
A control method and zero-gravity technology, applied in the direction of program control manipulators, manufacturing tools, claw arms, etc., can solve the problems of difficult to obtain trajectory planning points, low programming and teaching efficiency, high cost, and improve programming efficiency and quality. Maintenance The effect of convenient and quick upgrade and high efficiency of programming and teaching
- Summary
- Abstract
- Description
- Claims
- Application Information
AI Technical Summary
Problems solved by technology
Method used
Image
Examples
Embodiment Construction
[0026] The technical solutions in the embodiments of the present invention will be clearly and completely described below in conjunction with the accompanying drawings. Apparently, the described embodiments are only some of the embodiments of the present invention, not all of them. Based on the embodiments of the present invention, all other embodiments obtained by persons of ordinary skill in the art without making creative efforts belong to the protection scope of the present invention.
[0027] see figure 1 , a zero-gravity control method without torque sensing, comprising the following steps;
[0028] Step 1: Obtain the absolute position parameter pulse value of each joint of the mechanical arm through the absolute encoder, and convert the motor pulse amount into the pulse amount based on the origin of the Cartesian coordinate system;
[0029] Step 2: Iteratively calculate the instantaneous velocity value and instantaneous acceleration value according to the definition ca...
PUM
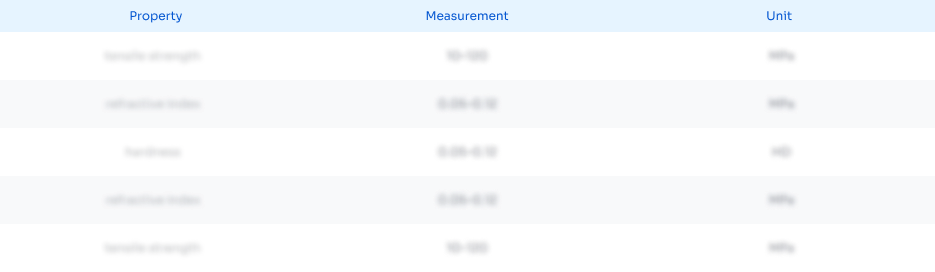
Abstract
Description
Claims
Application Information

- Generate Ideas
- Intellectual Property
- Life Sciences
- Materials
- Tech Scout
- Unparalleled Data Quality
- Higher Quality Content
- 60% Fewer Hallucinations
Browse by: Latest US Patents, China's latest patents, Technical Efficacy Thesaurus, Application Domain, Technology Topic, Popular Technical Reports.
© 2025 PatSnap. All rights reserved.Legal|Privacy policy|Modern Slavery Act Transparency Statement|Sitemap|About US| Contact US: help@patsnap.com