A Pile Length Detection Method Based on Zero Offset Method
A technology with zero offset distance and detection method, which is applied in the direction of foundation structure test, measurement device, foundation structure engineering, etc., can solve the problems such as inability to collect data at the pile end, limited space for data collection, and restricting the development of observation methods, etc. Achieve the effect of short detection time, strong practicability and wide application range
- Summary
- Abstract
- Description
- Claims
- Application Information
AI Technical Summary
Problems solved by technology
Method used
Image
Examples
Embodiment Construction
[0026] The present invention will be further described in detail below in conjunction with the accompanying drawings and specific embodiments.
[0027] Such as figure 1 Shown is a pile length detection method based on the zero offset method, comprising the following steps:
[0028] 1) Measuring point layout: multiple excitation points and multiple receiving points are arranged at intervals at different elevations along the axis of the pile; for example figure 2 As shown, the multiple excitation points are the excitation point J1, the excitation point J2... the excitation point Jn arranged sequentially from bottom to top, wherein n>3; the multiple receiving points are sequentially arranged from bottom to top Uniformly arranged receiving point R1, receiving point R2...receiving point Rn, wherein, n>3; any adjacent two of the excitation point J1, excitation point J2...excitation point Jn are equally spaced or not Arranged at equal intervals; the excitation point J1, the excita...
PUM
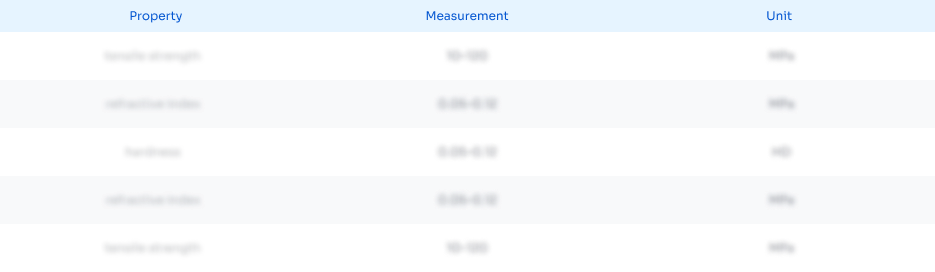
Abstract
Description
Claims
Application Information

- Generate Ideas
- Intellectual Property
- Life Sciences
- Materials
- Tech Scout
- Unparalleled Data Quality
- Higher Quality Content
- 60% Fewer Hallucinations
Browse by: Latest US Patents, China's latest patents, Technical Efficacy Thesaurus, Application Domain, Technology Topic, Popular Technical Reports.
© 2025 PatSnap. All rights reserved.Legal|Privacy policy|Modern Slavery Act Transparency Statement|Sitemap|About US| Contact US: help@patsnap.com