Preparation method of multiphase nano-scale composite carbon material
A composite carbon, nano-scale technology, applied in chemical instruments and methods, fibrous fillers, inorganic pigment treatment, etc., can solve the problems of poor dispersion, poor wear resistance and electrical conductivity of tread rubber, and high heat generation, and improve electrical conductivity. The effect of resistance and wear resistance
- Summary
- Abstract
- Description
- Claims
- Application Information
AI Technical Summary
Problems solved by technology
Method used
Image
Examples
Example Embodiment
[0018] Example 1
[0019] 1) Preparation of graphene nano-powder: graphite powder, a polyoxyethylene ether solution with a mass concentration of 1.5% is mixed into a ball milling tank, the mass ratio of graphite powder to polyoxyethylene ether is 1:100, and the size of the ball milling tank is 20cm , The grinding ball specification is 10mm, the ball mill speed is 600rpm, the ball milling time is 20h, and the upper black solution is poured out after standing for 24h. The solid obtained after washing and suction filtration of this solution is put into the muffle furnace, heated at 650℃, and kept for a period of time Until the residual active agent is carbonized, a graphene nano-powder with a layer number of less than 10 layers is obtained; the graphene powder is scanned by an electron microscope, and the scanned picture is shown figure 1 ;
[0020] 2) Grafting reaction: Put the graphene powder and appropriate amount of carbon black into a grafting reactor with stirring teeth, add a 1...
Example Embodiment
[0023] Example 2
[0024] 1) Graphene nano-powder preparation: graphite powder, 0.1% sodium dodecylbenzene sulfonate solution with a mass concentration of 0.1% is mixed into a ball milling tank, the mass ratio of graphite powder to surfactant is 1:50, ball milling The size of the tank is 20cm, the size of the grinding ball is 12mm, the speed of the ball mill is 200rpm, and the milling time is 10h. After standing for 24h, the upper layer of black solution is poured out. After washing and filtering the solution, the solid obtained is placed in a muffle furnace and heated to 100℃ , Keep for a period of time until the residual active agent is carbonized to obtain graphene nano-powder with less than 10 layers;
[0025] 2) Grafting reaction: Put the graphene powder and an appropriate amount of carbon black into a grafting reactor with stirring teeth, and add 4,4'-azobis(4-cyanovaleric acid with a mass concentration of 1%) ) Polyethylene glycol ester aqueous solution, the mass ratio of g...
Example Embodiment
[0027] Example 3
[0028] 1) Graphene nano-powder preparation: graphite powder, 3% octylphenol polyoxyethylene ether solution with a mass concentration of 3% is mixed into the ball mill tank, the mass ratio of graphite powder to surfactant is 1:150, the size of the ball mill tank The size of the grinding ball is 20cm, the size of the grinding ball is 12mm, the speed of the ball mill is 1000rpm, and the ball milling time is 30h. After standing for 24h, the upper layer of black solution is poured out. A period of time until the residual active agent is carbonized to obtain graphene nano-powder with less than 10 layers;
[0029] 2) Grafting reaction: Put graphene powder and appropriate amount of carbon black into a grafting reactor with stirring teeth, and add 3-chloropropyltrimethoxysilane aqueous solution with a mass concentration of 3%, graphene powder The mass ratio with carbon black and coupling agent is 1:50:20, the temperature of the reactor is 150℃, and the pressure is 5kg / cm...
PUM
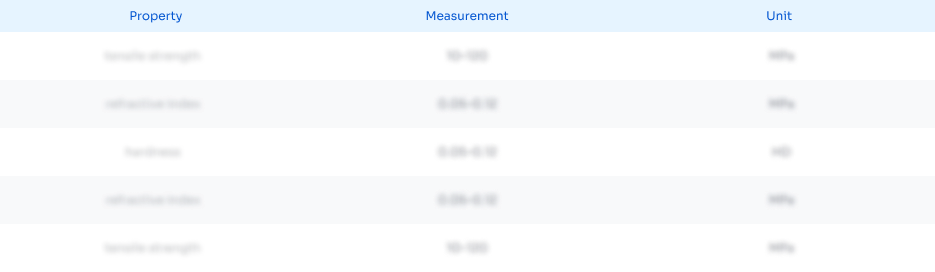
Abstract
Description
Claims
Application Information

- R&D Engineer
- R&D Manager
- IP Professional
- Industry Leading Data Capabilities
- Powerful AI technology
- Patent DNA Extraction
Browse by: Latest US Patents, China's latest patents, Technical Efficacy Thesaurus, Application Domain, Technology Topic, Popular Technical Reports.
© 2024 PatSnap. All rights reserved.Legal|Privacy policy|Modern Slavery Act Transparency Statement|Sitemap|About US| Contact US: help@patsnap.com