Pneumatic two-way bending soft body driver based on paper folding structures
A technology of software driver and origami structure, which is applied in manipulators, program-controlled manipulators, manufacturing tools, etc., can solve the problems of small end force, uneven wall thickness, and large end force of fiber-reinforced type, and achieve the effect of large end force
- Summary
- Abstract
- Description
- Claims
- Application Information
AI Technical Summary
Problems solved by technology
Method used
Image
Examples
Embodiment Construction
[0025] In order to make the object, technical solution and advantages of the present invention clearer, the present invention will be further described in detail below in conjunction with examples. It should be understood that the specific embodiments described here are only used to explain the present invention, not to limit the present invention.
[0026] A kind of pneumatic two-way bending software driver based on origami structure of the present invention, such as Figure 5 As shown, it includes a constraining layer structure 1 and two deforming layer structures with the same structure, that is, the first deforming layer structure 2 and the second deforming layer structure 3, and the first deforming layer structure 2 and the second deforming layer structure 3 are symmetrically arranged on Limit layer structure 1 on both sides. The first deformation layer structure 2 and the restriction layer structure 1 form the first driving unit, and the first driving unit realizes down...
PUM
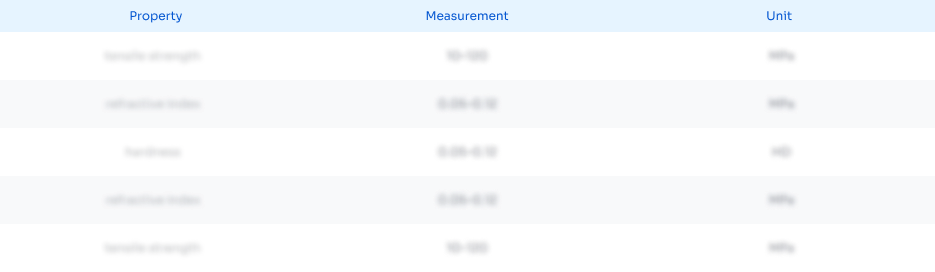
Abstract
Description
Claims
Application Information

- Generate Ideas
- Intellectual Property
- Life Sciences
- Materials
- Tech Scout
- Unparalleled Data Quality
- Higher Quality Content
- 60% Fewer Hallucinations
Browse by: Latest US Patents, China's latest patents, Technical Efficacy Thesaurus, Application Domain, Technology Topic, Popular Technical Reports.
© 2025 PatSnap. All rights reserved.Legal|Privacy policy|Modern Slavery Act Transparency Statement|Sitemap|About US| Contact US: help@patsnap.com