Double-layer combination flap valve
A flap valve, double-layer technology, applied in the direction of conveyor objects, transportation and packaging, can solve the problems of aggravating material accumulation, increase production, installation cost, poor stability, etc., to avoid material accumulation, enhance sealing performance, and stabilize strong effect
- Summary
- Abstract
- Description
- Claims
- Application Information
AI Technical Summary
Problems solved by technology
Method used
Image
Examples
Embodiment Construction
[0039] As shown in the figure: a double-layer combined flap valve, including a first blanking valve and a second blanking valve, the first blanking valve is located on the upper layer, and the second blanking valve is located on the lower layer; the first blanking valve It includes an upper cylinder, a funnel, a corner, a lever, and a left and right flap; the lever can be controlled to rotate through the corner, thereby driving the left and right flaps to rotate, thereby opening or closing the first blanking valve. A funnel is arranged on the top of the cylinder, which is convenient for receiving materials; the second blanking valve includes a lower cylinder, a baffle, a spring, a roulette, a support rod, a flange, a straight cylinder, a cylinder shoulder, a cylinder, a discharge port, a leaf Plate, comb tooth, telescopic rod, fulcrum, conical disc, damping ring, servo motor, bracket, ferrule, rotating ring, protrusion; The first blanking valve and the second blanking valve ar...
PUM
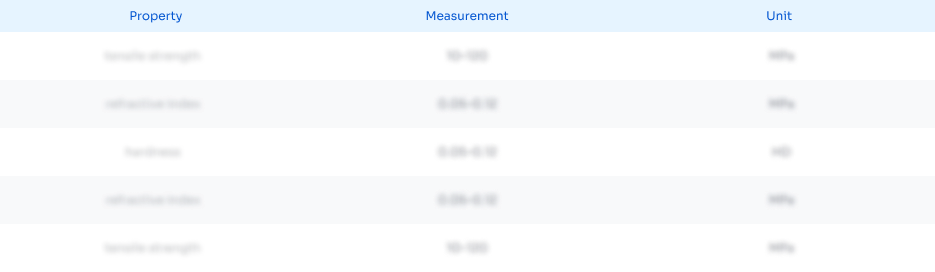
Abstract
Description
Claims
Application Information

- R&D
- Intellectual Property
- Life Sciences
- Materials
- Tech Scout
- Unparalleled Data Quality
- Higher Quality Content
- 60% Fewer Hallucinations
Browse by: Latest US Patents, China's latest patents, Technical Efficacy Thesaurus, Application Domain, Technology Topic, Popular Technical Reports.
© 2025 PatSnap. All rights reserved.Legal|Privacy policy|Modern Slavery Act Transparency Statement|Sitemap|About US| Contact US: help@patsnap.com