Method for detecting weld joint of stiffening plate
A welding seam detection and reinforcing plate technology is applied in the direction of using liquid/vacuum for liquid tightness measurement, etc., which can solve the problems of troublesome, difficult operation, and small diameter of the leakage signal indicating hole, so as to achieve convenient operation and reduce detection costs. , The effect of leak detection is convenient for operation
- Summary
- Abstract
- Description
- Claims
- Application Information
AI Technical Summary
Problems solved by technology
Method used
Image
Examples
Embodiment 1
[0023] The welding seam detection method of the reinforcing plate of the present invention comprises the following steps:
[0024] figure 1 It is a structural schematic diagram of a reinforcing plate according to an embodiment of the present invention.
[0025] a. Before the reinforcement plate is welded to the pipe member, weld a stainless steel instrument tube 2 with a length of 200mm and a diameter slightly larger than the diameter of the leakage signal indication hole 1 of the reinforcement plate on the leakage signal indication hole 1 of the reinforcement plate, so as to pass through the stainless steel instrument The pipe is used to feed or discharge air to the leak signal indicating hole. figure 2 It is a schematic diagram of welding a stainless steel instrument tube on a reinforcing plate according to an embodiment of the present invention. After the stainless steel instrument tube is welded on the leakage signal indication hole, the reinforcement plate of the stora...
PUM
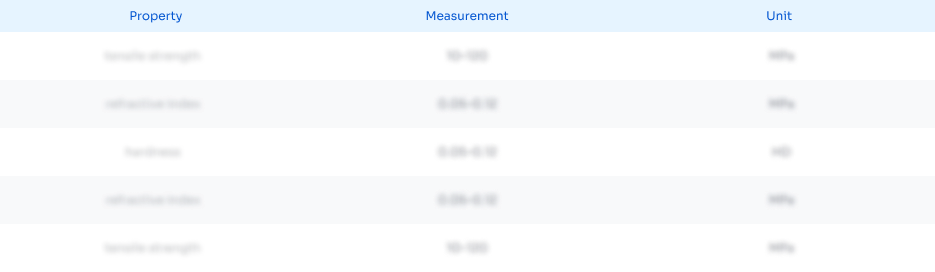
Abstract
Description
Claims
Application Information

- R&D Engineer
- R&D Manager
- IP Professional
- Industry Leading Data Capabilities
- Powerful AI technology
- Patent DNA Extraction
Browse by: Latest US Patents, China's latest patents, Technical Efficacy Thesaurus, Application Domain, Technology Topic, Popular Technical Reports.
© 2024 PatSnap. All rights reserved.Legal|Privacy policy|Modern Slavery Act Transparency Statement|Sitemap|About US| Contact US: help@patsnap.com