Railway vehicle inspection and maintenance assisting robot
A rail vehicle and robot technology, applied in the field of rail vehicle maintenance auxiliary robots, can solve the problems of wide area to be inspected, hidden dangers of vehicle operation safety, strong accidental failure, etc., to improve maintenance quality and reliability, reduce labor intensity, improve The effect of information level
- Summary
- Abstract
- Description
- Claims
- Application Information
AI Technical Summary
Problems solved by technology
Method used
Image
Examples
Embodiment Construction
[0032] In order to make the purpose, technical solution and advantages of the present invention clearer, the embodiments of the present invention will be further described in detail below in conjunction with the accompanying drawings.
[0033] See Figure 1 to Figure 4 , The rail vehicle maintenance auxiliary robot 100 of the present invention includes a robot body 11, an action execution device 12, a walking device 13, an image acquisition system 14, a control system 15, an image processing system 16, a video monitoring device 17, a positioning system 18, and a safety protection device 19. Power supply device 20 , monitoring system 21 , internal temperature and humidity control device 22 , walking track 23 , and remote control terminal 24 .
[0034] The robot body 11 is used to carry and install relevant components of the rail vehicle maintenance assistance robot 100 .
[0035] The action executing device 12 includes a lifting device 121 , a translation device 122 , and a mu...
PUM
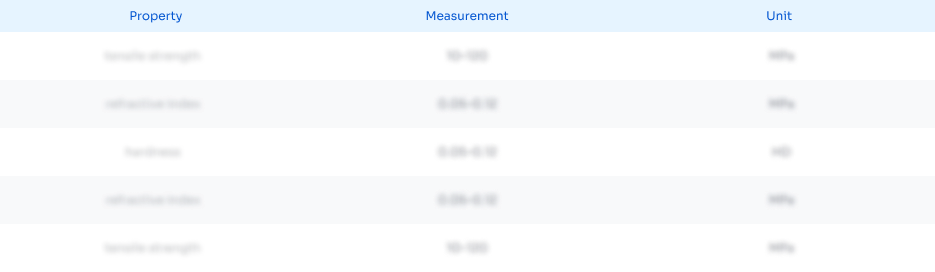
Abstract
Description
Claims
Application Information

- R&D Engineer
- R&D Manager
- IP Professional
- Industry Leading Data Capabilities
- Powerful AI technology
- Patent DNA Extraction
Browse by: Latest US Patents, China's latest patents, Technical Efficacy Thesaurus, Application Domain, Technology Topic, Popular Technical Reports.
© 2024 PatSnap. All rights reserved.Legal|Privacy policy|Modern Slavery Act Transparency Statement|Sitemap|About US| Contact US: help@patsnap.com