cotton thread production equipment
A technology for production equipment and cotton thread, applied in textiles and papermaking, fiber processing, deburring devices, etc., can solve the problem of high replacement costs, achieve the effects of saving replacement costs, simple operation, and eliminating potential safety hazards
- Summary
- Abstract
- Description
- Claims
- Application Information
AI Technical Summary
Problems solved by technology
Method used
Image
Examples
Embodiment 1
[0028] This embodiment is basically as figure 1 As shown, the cotton thread production equipment includes a carding machine housing 1, a rotating roller 2 and a motor 3 for driving the rotating roller 2, and the rotating roller 2 is connected in rotation on the front and rear side walls of the carding machine housing 1, and the motor The output end of 3 is fixedly connected with rotating shaft 4 coaxially, and rotating shaft 4 is fixedly connected with rotating roller 2 coaxially. combine figure 2 As shown, a first cavity 5 and a second cavity 6 are provided in the rotating roller 2, and the first cavity 5 and the second cavity 6 are all arranged along the circumferential direction of the rotating roller 2, and the first cavity 5 and the second cavity The cavity 6 divides the rotating roller 2 into a first roller body 201 , a second roller body 202 and a third roller body 203 .
[0029] The first elastic airbag 7 is fixedly installed on the inner peripheral wall of the firs...
Embodiment 2
[0039] Such as figure 1 , figure 2 and Figure 4 As shown, the difference from Embodiment 1 is that the top end of the first air outlet pipe 24 is threadedly connected with a second air outlet pipe 34, the upper end of the second air outlet pipe 34 communicates with a third elastic air bag 35, and the third elastic air bag 35 communicates with a Air release pipe 36 and air delivery pipe 37, air pressure valve 38 and the third air valve 39 are installed on the air release pipe 36, the third air valve 39 is in normally open state, the fourth air valve 40 is installed on the air delivery pipe 37, the fourth air valve 40 is in a normally closed state.
[0040] During specific work, the gas in the right chamber 22 is stored in the third elastic air bag 35 through the first air outlet pipe 24 and the second air outlet pipe 34, and when the internal pressure of the third elastic air bag 35 gradually increases to the threshold value of the air pressure valve 38 At this time, the g...
PUM
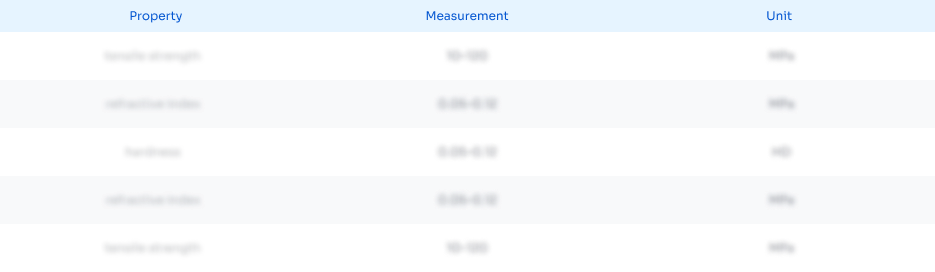
Abstract
Description
Claims
Application Information

- Generate Ideas
- Intellectual Property
- Life Sciences
- Materials
- Tech Scout
- Unparalleled Data Quality
- Higher Quality Content
- 60% Fewer Hallucinations
Browse by: Latest US Patents, China's latest patents, Technical Efficacy Thesaurus, Application Domain, Technology Topic, Popular Technical Reports.
© 2025 PatSnap. All rights reserved.Legal|Privacy policy|Modern Slavery Act Transparency Statement|Sitemap|About US| Contact US: help@patsnap.com