A Flywheel Stiffness Parameter Extraction Method Based on Microvibration Waterfall Diagram
A parameter extraction and micro-vibration technology, applied in the testing of mechanical components, testing of machine/structural components, instruments, etc., can solve the need to improve the accuracy of the model, provide active guidance for the scientific research and production of flywheel products, and stay in theoretical analysis. And other issues
- Summary
- Abstract
- Description
- Claims
- Application Information
AI Technical Summary
Problems solved by technology
Method used
Image
Examples
Embodiment Construction
[0054] The method of the invention firstly establishes a dynamic model of a single-end fixedly supported flywheel rotor, and obtains the micro-vibration transfer function of the flywheel rotor. Secondly, using robust regression to fit the frequency-speed whirl curve in the micro-vibration waterfall diagram, it is four dominant frequency-speed segmental functions; finally, substituting the segmental functions into the theoretical characteristic polynomial of the transfer function, through The integral of its weighted sum of squares in the full speed range is minimized, and the best approximation model parameters are identified.
[0055] The invention provides a flywheel stiffness parameter extraction method based on a micro-vibration waterfall diagram, comprising the following steps:
[0056] (1) Establish flywheel coordinate system
[0057] Such as figure 1 As shown, the inertial coordinate system F I :oxyz. Its origin o is located at the center of the root of the support ...
PUM
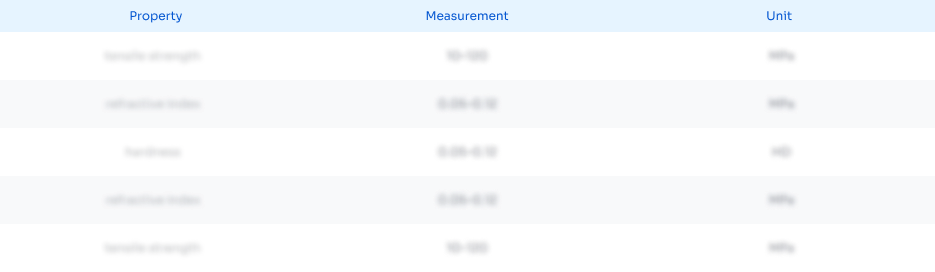
Abstract
Description
Claims
Application Information

- R&D
- Intellectual Property
- Life Sciences
- Materials
- Tech Scout
- Unparalleled Data Quality
- Higher Quality Content
- 60% Fewer Hallucinations
Browse by: Latest US Patents, China's latest patents, Technical Efficacy Thesaurus, Application Domain, Technology Topic, Popular Technical Reports.
© 2025 PatSnap. All rights reserved.Legal|Privacy policy|Modern Slavery Act Transparency Statement|Sitemap|About US| Contact US: help@patsnap.com