An elastoplastic damage finite element method considering the coupling of elastoplasticity and damage in composite materials
A composite material and elastoplastic technology, which is applied in the direction of analyzing materials, using stable tension/pressure to test material strength, strength characteristics, etc., can solve the problems of increasing the difficulty, shortage, and non-consideration of composite material structures
- Summary
- Abstract
- Description
- Claims
- Application Information
AI Technical Summary
Problems solved by technology
Method used
Image
Examples
Embodiment
[0040] combine figure 1 , an elastoplastic damage finite element subroutine algorithm considering the coupling effect of elastoplasticity and damage of fiber-reinforced resin matrix composites, including the following steps:
[0041] Step 1, start the current incremental step, read the convergence state quantity at the previous moment and the strain increment in the current incremental step; specifically:
[0042] Read the previous incremental step ie tn The effective stress at the integration point of the material element at time Strain ε n , plastic strain Equivalent plastic strain value Damage state quantity D n And the current incremental step is the n+1th incremental step t n ~t n+1 time strain increment
[0043] effective stress strain plastic strain Damage state quantity D n for
[0044]
[0045] Among them, d 1 , d 2 are the damage variables representing fiber damage and matrix damage, respectively, d 12 , d 23 , d 13 is the damage variable ...
PUM
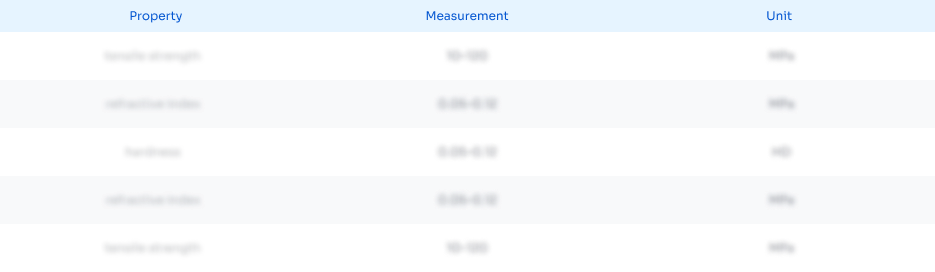
Abstract
Description
Claims
Application Information

- Generate Ideas
- Intellectual Property
- Life Sciences
- Materials
- Tech Scout
- Unparalleled Data Quality
- Higher Quality Content
- 60% Fewer Hallucinations
Browse by: Latest US Patents, China's latest patents, Technical Efficacy Thesaurus, Application Domain, Technology Topic, Popular Technical Reports.
© 2025 PatSnap. All rights reserved.Legal|Privacy policy|Modern Slavery Act Transparency Statement|Sitemap|About US| Contact US: help@patsnap.com