Visual sense measuring instrument and visual sense measuring method
A visual measurement and instrument technology, applied in the field of visual measurement, can solve problems such as misalignment, narrow field of view, and undetermined positional relationship, and achieve the effects of improving accuracy and solving horizontal attitude and height difference
- Summary
- Abstract
- Description
- Claims
- Application Information
AI Technical Summary
Problems solved by technology
Method used
Image
Examples
Embodiment Construction
[0049] The present application will be described in further detail below through specific embodiments in conjunction with the accompanying drawings. The present application can be realized in many different forms, and is not limited to the implementation manner described in this embodiment. The purpose of providing the following specific embodiments is to facilitate a clearer and more thorough understanding of the disclosure of the present application, wherein the words indicating orientation such as up, down, left, and right are only for the positions of the structures shown in the corresponding drawings.
[0050] However, those skilled in the art may recognize that description of one or more of the specific details may be omitted, or other methods, components or materials may also be used. In some instances, some implementations were not described or described in detail.
[0051] In addition, the technical features and technical solutions described herein can also be combin...
PUM
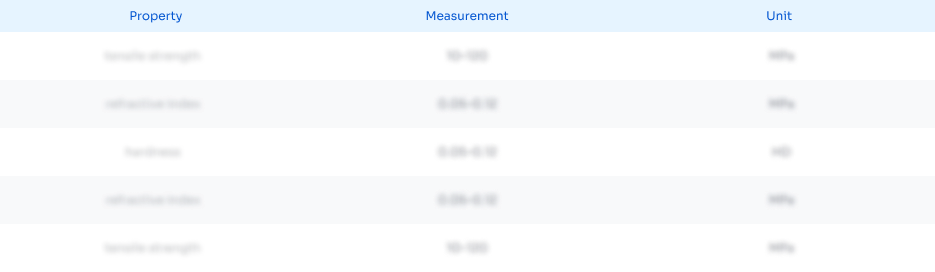
Abstract
Description
Claims
Application Information

- R&D
- Intellectual Property
- Life Sciences
- Materials
- Tech Scout
- Unparalleled Data Quality
- Higher Quality Content
- 60% Fewer Hallucinations
Browse by: Latest US Patents, China's latest patents, Technical Efficacy Thesaurus, Application Domain, Technology Topic, Popular Technical Reports.
© 2025 PatSnap. All rights reserved.Legal|Privacy policy|Modern Slavery Act Transparency Statement|Sitemap|About US| Contact US: help@patsnap.com