Fixture used for multistage overall blade disk electron beam welding
An electron beam welding and integral blisk technology, applied in electron beam welding equipment, welding equipment, welding equipment and other directions, can solve the problems of large deformation and inability to meet the requirements of use, achieve convenient operation and use, reduce cleaning workload, improve The effect of welding productivity
- Summary
- Abstract
- Description
- Claims
- Application Information
AI Technical Summary
Problems solved by technology
Method used
Image
Examples
Embodiment
[0028] A jig for electron beam welding of multi-stage blisks provided in this embodiment is designed according to the three-stage blisks of a certain type of engine. The central position of No. 2 blisk, No. 2 blisk and No. 3 blisk, see figure 1 , so the structure of the designed fixture is as follows figure 2 As shown, it is specifically composed of base 1, fixed column 3, lower fixed spacer 6, upper fixed spacer 9, cover plate 12, compression nut 13 and hoisting earring 14, fixed column 3, lower fixed spacer 6, The upper fixed spacer 9, the cover plate 12, and the compression nut 13 are sequentially assembled on the base 1 with the No. 1, No. 2 and No. 3 integral blisks to be welded from bottom to top, and the hoisting earrings 14 are fixedly connected to the fixed column 3 upper end, see Figure 5 .
[0029]The base 1 is a circular disc with a coaxial limiting boss on its upper surface. The diameter of the boss matches the inner diameter of the hole on the lower end of t...
PUM
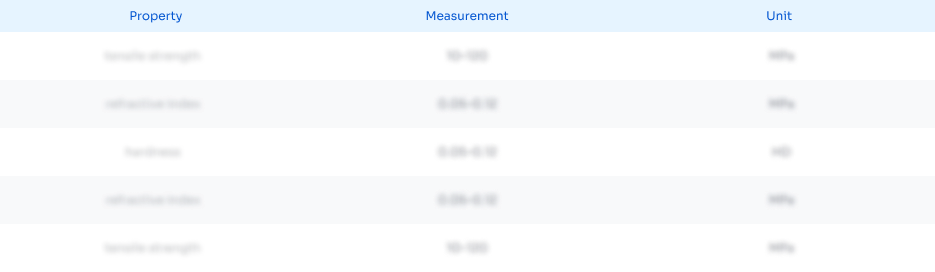
Abstract
Description
Claims
Application Information

- R&D Engineer
- R&D Manager
- IP Professional
- Industry Leading Data Capabilities
- Powerful AI technology
- Patent DNA Extraction
Browse by: Latest US Patents, China's latest patents, Technical Efficacy Thesaurus, Application Domain, Technology Topic, Popular Technical Reports.
© 2024 PatSnap. All rights reserved.Legal|Privacy policy|Modern Slavery Act Transparency Statement|Sitemap|About US| Contact US: help@patsnap.com