Intelligent control system of thermal power unit
An intelligent control system, a technology for thermal power units, applied in control systems, control combustion, combustion methods, etc., can solve the problems of poor control logic adaptability, control logic adaptability and automation reduction, and increased labor intensity of power equipment operators. The effect of reducing system cost, reducing operation burden, and increasing service life
- Summary
- Abstract
- Description
- Claims
- Application Information
AI Technical Summary
Problems solved by technology
Method used
Image
Examples
Embodiment Construction
[0043] Hereinafter, preferred embodiments of the present invention will be described with reference to the drawings. Those skilled in the art should understand that these embodiments are only used to explain the technical principles of the present invention and are not intended to limit the protection scope of the present invention.
[0044] See attached figure 1 , figure 1 Illustratively shows the structure diagram of the intelligent control system of the thermal power unit in this embodiment. Such as figure 1 As shown, the intelligent control system of the thermal power unit in this embodiment may include a fuel feedforward control module 11, a primary fan control module 12, a blower control module 13, and a superheated steam temperature control module 14. Wherein, the fuel feedforward control module 11 is configured to adjust the fuel control bias amount according to the load state, and modify the fuel control target value according to the adjusted fuel control bias amount. T...
PUM
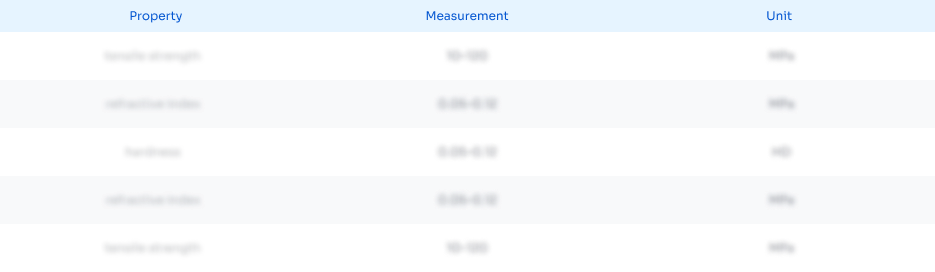
Abstract
Description
Claims
Application Information

- R&D Engineer
- R&D Manager
- IP Professional
- Industry Leading Data Capabilities
- Powerful AI technology
- Patent DNA Extraction
Browse by: Latest US Patents, China's latest patents, Technical Efficacy Thesaurus, Application Domain, Technology Topic, Popular Technical Reports.
© 2024 PatSnap. All rights reserved.Legal|Privacy policy|Modern Slavery Act Transparency Statement|Sitemap|About US| Contact US: help@patsnap.com