Rigid reinforced multi-degree-of-freedom platform based on mechanic-electronic-hydraulic integration
An electro-hydraulic, degree-of-freedom technology, used in the testing of mechanical components, the testing of machine/structural components, the testing of machine gears/transmission mechanism, etc., can solve the problem of vibration control of the transmission mechanism, and the one-time installation accuracy requirements are too high , The adjustment of multiple degrees of freedom cannot be realized, and the effect of meeting the requirements of automatic positioning and automatic locking, ensuring the requirements of stability and reliability, and reducing the requirements of positioning accuracy can be achieved.
- Summary
- Abstract
- Description
- Claims
- Application Information
AI Technical Summary
Problems solved by technology
Method used
Image
Examples
Embodiment Construction
[0028] The present invention will be further described below in conjunction with accompanying drawing and embodiment:
[0029] Such as figure 1As shown, a mechanical-electric-hydraulic integrated rigidity-enhanced multi-degree-of-freedom platform, the entire platform is a modular superimposed arrangement, and the platform includes a basic platform, X-axis platform 1, X-axis driving device 2, Y-axis platform 3, and Y-axis driving device 4. Z-axis platform 10, Z-axis platform guard plate 11, Z-axis platform support plate 41 and Z-axis lifting device 12; X-axis platform 1 is fixedly connected with the basic platform, and the fixed end of X-axis driving device 2 is fixed on the X-axis platform 1, the moving end of the X-axis driving device 2 is connected to the Y-axis platform 3; the fixed end of the Y-axis driving device 4 is fixed on the Y-axis platform 3, and the moving end is connected to the Z-axis platform supporting plate 41; the Z-axis platform guard plate 11 is fixed aro...
PUM
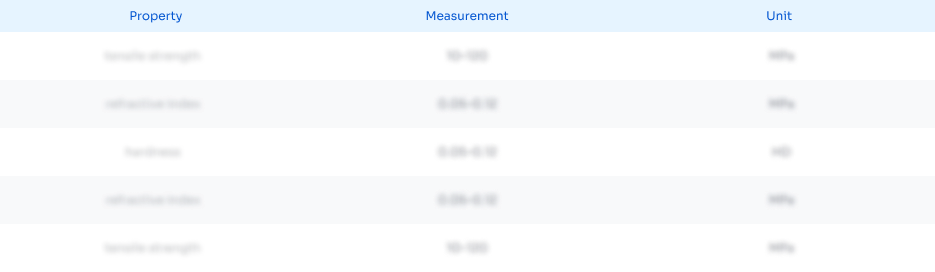
Abstract
Description
Claims
Application Information

- R&D
- Intellectual Property
- Life Sciences
- Materials
- Tech Scout
- Unparalleled Data Quality
- Higher Quality Content
- 60% Fewer Hallucinations
Browse by: Latest US Patents, China's latest patents, Technical Efficacy Thesaurus, Application Domain, Technology Topic, Popular Technical Reports.
© 2025 PatSnap. All rights reserved.Legal|Privacy policy|Modern Slavery Act Transparency Statement|Sitemap|About US| Contact US: help@patsnap.com