A method of using a trailer frame component assembly and welding system
A welding system and component technology, applied in welding equipment, welding equipment, vehicle components, etc., can solve problems such as potential safety hazards, frame assembly errors, and low weld strength, so as to avoid potential safety hazards, prevent bump deformation, reduce The effect of labor intensity
- Summary
- Abstract
- Description
- Claims
- Application Information
AI Technical Summary
Problems solved by technology
Method used
Image
Examples
Embodiment Construction
[0027] The present invention will be further described below in conjunction with accompanying drawing (be described ahead with the traction direction of tractor below).
[0028] Such as figure 1 , figure 2 As shown, the trailer frame assembly assembly welding system used in the method of using the trailer frame assembly assembly welding system includes a support frame 1, a turning shaft 2, a workpiece support part 3 and an electric control device.
[0029] The support frame 1 is symmetrically arranged in two pieces in the front and back directions, and is fixedly installed on the ground.
[0030] Described overturning shaft 2 is arranged as two pieces, and two overturning shafts 2 are concentrically arranged, and one end of two overturning shafts 2 is installed on the upper inner surface of support frame 1 through the bearing seat, and at least one overturning shaft 2 is provided with The supporting frame 1 or the overturning drive device 21 on the ground can drive the over...
PUM
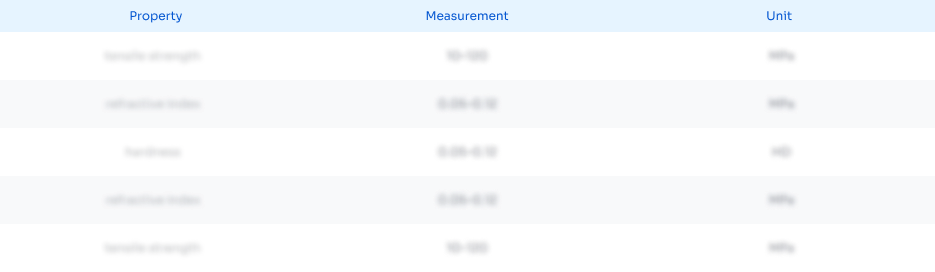
Abstract
Description
Claims
Application Information

- R&D Engineer
- R&D Manager
- IP Professional
- Industry Leading Data Capabilities
- Powerful AI technology
- Patent DNA Extraction
Browse by: Latest US Patents, China's latest patents, Technical Efficacy Thesaurus, Application Domain, Technology Topic, Popular Technical Reports.
© 2024 PatSnap. All rights reserved.Legal|Privacy policy|Modern Slavery Act Transparency Statement|Sitemap|About US| Contact US: help@patsnap.com