Real-time simulation modeling method for variable geometric split axle type combustion gas turbine
A gas turbine, real-time simulation technology, applied in neural learning methods, design optimization/simulation, biological neural network models, etc., can solve problems such as difficulty in directly establishing simulation models, poor real-time performance of nonlinear models, and difficulty in ensuring simulation accuracy, to avoid Thermal calculation of working fluid, guarantee of simulation accuracy, and simplified establishment
- Summary
- Abstract
- Description
- Claims
- Application Information
AI Technical Summary
Problems solved by technology
Method used
Image
Examples
Embodiment Construction
[0030] In order to make the object, technical solution and advantages of the present invention clearer, the following describes the present invention in further detail with reference to the accompanying drawings and examples, so that the advantages and features of the present invention can be more easily understood by those skilled in the art. It should be noted that the following descriptions are only preferred embodiments of the present invention, and therefore do not limit the protection scope of the present invention. In fact, it will be apparent to those skilled in the art that various modifications and variations can be made in the present invention without departing from the scope or spirit of the invention. For example, features illustrated or described as part of one embodiment can be used with another embodiment to yield a still further embodiment. Therefore, it is intended that the present invention cover such modifications and variations as come within the scope of...
PUM
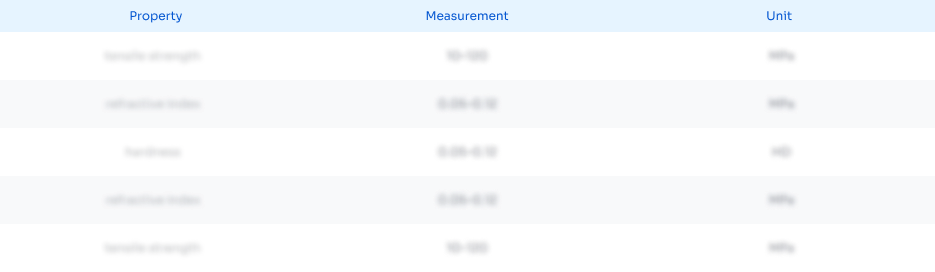
Abstract
Description
Claims
Application Information

- R&D Engineer
- R&D Manager
- IP Professional
- Industry Leading Data Capabilities
- Powerful AI technology
- Patent DNA Extraction
Browse by: Latest US Patents, China's latest patents, Technical Efficacy Thesaurus, Application Domain, Technology Topic, Popular Technical Reports.
© 2024 PatSnap. All rights reserved.Legal|Privacy policy|Modern Slavery Act Transparency Statement|Sitemap|About US| Contact US: help@patsnap.com