Positioning ultrasonic testing device and positioning ultrasonic testing method for curved welding component
A technology for ultrasonic testing and welding parts, which is used in measurement devices, material analysis using sonic/ultrasonic/infrasonic waves, instruments, etc. It can solve the problems of difficult to achieve quantitative ultrasonic testing of complex curved parts.
- Summary
- Abstract
- Description
- Claims
- Application Information
AI Technical Summary
Problems solved by technology
Method used
Image
Examples
Embodiment
[0078] A positioning ultrasonic detection method of a curved surface weldment based on a series-parallel hybrid mechanism, the specific implementation steps are as follows:
[0079] 1. Workpiece surface treatment: Before scanning the data, the surface of the vibration friction welding workpiece in the airbag area of the automobile dashboard is dedusted, degreased, and coated with coupling agent to reduce the interference of impurities on the surface of the workpiece to the ultrasonic signal.
[0080] 2. Input the surface shape data of the scanned workpiece, and plan the placement position of the base of the multi-link robotic arm. The three-dimensional surface STP format data of the vibration friction welding workpiece in the airbag area of the automobile dashboard is imported into the system through the USB interface, and the placement position of the multi-link manipulator base is planned through the spatial position that the ultrasonic probe can reach. The spatial dimen...
PUM
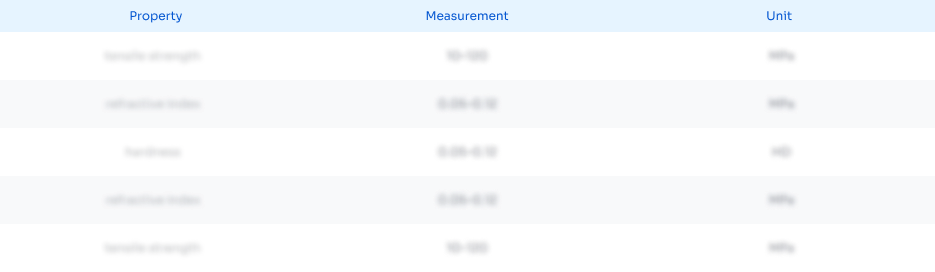
Abstract
Description
Claims
Application Information

- R&D
- Intellectual Property
- Life Sciences
- Materials
- Tech Scout
- Unparalleled Data Quality
- Higher Quality Content
- 60% Fewer Hallucinations
Browse by: Latest US Patents, China's latest patents, Technical Efficacy Thesaurus, Application Domain, Technology Topic, Popular Technical Reports.
© 2025 PatSnap. All rights reserved.Legal|Privacy policy|Modern Slavery Act Transparency Statement|Sitemap|About US| Contact US: help@patsnap.com