Integrated load limiting valve and actuator with mechanically adjustable output force
A kind of actuator and mechanical technology, applied in the field of servo loading system, can solve the problems of easy self-excited vibration, large size, inconvenient installation, etc., to solve the problem of interchangeability, not easy to self-excited vibration, accurate and reliable protection Effect
- Summary
- Abstract
- Description
- Claims
- Application Information
AI Technical Summary
Problems solved by technology
Method used
Image
Examples
Embodiment 1
[0026] Example 1, such as figure 1 , a load limiting integrated valve 4, including a valve body 3, a first pilot relief valve 1 and a second pilot relief valve 2 are installed on the valve body, the oil discharge of the first pilot relief valve 1 The port L1 communicates with the oil inlet B of the second pilot relief valve, and the oil discharge port L2 of the second pilot relief valve communicates with the oil inlet A of the first pilot relief valve.
[0027] The load limiting integrated valve 4 of this embodiment can be directly installed on the actuator 5. During installation, the overflow port R1 of the first pilot relief valve and the relief port R2 of the second pilot relief valve are respectively The oil return port R of the valve body communicates with the total oil return circuit of the actuator, the oil inlet A of the first pilot relief valve 1 communicates with the first load chamber of the actuator, and the second pilot The oil inlet B of the type relief valve 2 ...
Embodiment 2
[0030] Embodiment 2, an actuator, including a first load chamber, a second load chamber, and a total oil return circuit, and the actuator also includes a first pilot relief valve 1 and a second pilot relief valve Valve 2, the drain port L1 of the first pilot relief valve 1 communicates with the oil inlet B of the second pilot relief valve, and the drain port L2 of the second pilot relief valve communicates with the first The oil inlet A of the pilot relief valve is connected to eliminate the influence of the change of load pressure on the control accuracy; the relief port R1 of the first pilot relief valve and the relief port of the second pilot relief valve R2 communicates with the main oil return circuit of the servo actuator through the oil return port R of the valve body, and the oil inlet A of the first pilot relief valve 1 communicates with the first load chamber of the actuator. The oil inlet B of the second pilot relief valve 2 communicates with the second load chamber...
Embodiment 3
[0033] The difference between Embodiment 3 and Embodiment 2 is that the shape and installation method of the valve body are different, and the oil inlet A of the first pilot relief valve 1 is connected with the first load of the actuator through the pipeline and the pipe joint. The chambers communicate, and the oil inlet B of the second pilot relief valve 2 communicates with the second load chamber of the actuator through pipelines and pipe joints.
PUM
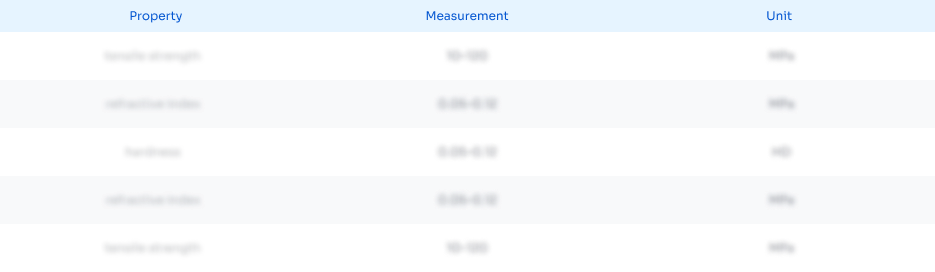
Abstract
Description
Claims
Application Information

- R&D
- Intellectual Property
- Life Sciences
- Materials
- Tech Scout
- Unparalleled Data Quality
- Higher Quality Content
- 60% Fewer Hallucinations
Browse by: Latest US Patents, China's latest patents, Technical Efficacy Thesaurus, Application Domain, Technology Topic, Popular Technical Reports.
© 2025 PatSnap. All rights reserved.Legal|Privacy policy|Modern Slavery Act Transparency Statement|Sitemap|About US| Contact US: help@patsnap.com