Method for designing local tempering induction coil of ultrahigh-strength steel threaded type workpiece based on finite element simulation
A technology of ultra-high-strength steel and induction coils, applied in design optimization/simulation, calculation, special data processing applications, etc., can solve problems such as low efficiency, cost, and long design cycle of induction heating power supply
- Summary
- Abstract
- Description
- Claims
- Application Information
AI Technical Summary
Problems solved by technology
Method used
Image
Examples
Embodiment Construction
[0034] Below in conjunction with accompanying drawing and embodiment the present invention is described in detail, but not limited thereto figure 1 It is a flowchart of a design method of an induction coil for local tempering of an ultra-high-strength steel threaded workpiece based on finite element simulation according to an embodiment of the present invention. Such as figure 1 As shown in Fig. 1, a geometric model is established according to the shape of the ultra-high-strength steel optical axis workpiece and the induction coil. After mesh division and material property loading, the finite element simulation of induction heating is carried out, and the simulated results are compared with the experimental measurement results. , if the two can be well matched, the next step is to design the induction coil for ultra-high-strength steel threaded workpieces. The induction coil for local tempering of threaded workpieces is designed from the shape factor, position factor and numb...
PUM
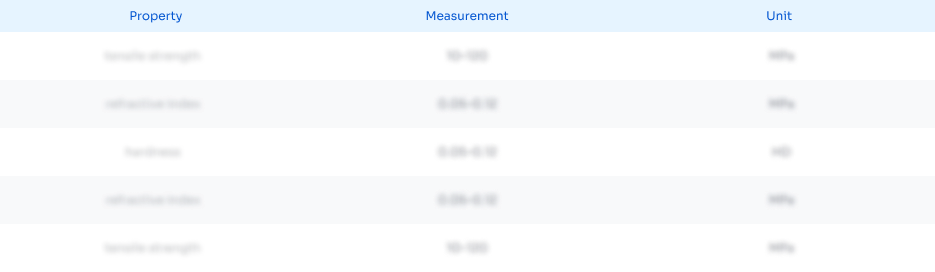
Abstract
Description
Claims
Application Information

- R&D
- Intellectual Property
- Life Sciences
- Materials
- Tech Scout
- Unparalleled Data Quality
- Higher Quality Content
- 60% Fewer Hallucinations
Browse by: Latest US Patents, China's latest patents, Technical Efficacy Thesaurus, Application Domain, Technology Topic, Popular Technical Reports.
© 2025 PatSnap. All rights reserved.Legal|Privacy policy|Modern Slavery Act Transparency Statement|Sitemap|About US| Contact US: help@patsnap.com