A Non-contact Dynamic Measurement System of Rotary Shaft Torque Based on High Precision Key Phase
A dynamic measurement, high-precision technology, applied in torque measurement, measurement device, power measurement, etc., can solve the problem of unsuitable dynamic torque measurement of rotating shaft, and achieve the effect of eliminating accumulated errors, improving measurement accuracy, and reducing timing errors.
- Summary
- Abstract
- Description
- Claims
- Application Information
AI Technical Summary
Problems solved by technology
Method used
Image
Examples
Embodiment 1
[0036] A non-contact dynamic measurement system for rotating shaft torque based on high-precision key phase, see figure 1 and figure 2 , the measuring system includes: a coding stripe 2 arranged on the measured rotating shaft 1,
[0037] Among them, a group of first coded stripes 2 are sprayed or pasted at a fixed distance on the tested rotating shaft 1, and the first coded stripes 2 are coded stripes with equal intervals between black and white (that is, there are two black and white alternated stripes on the tested rotating shaft 1). The first coding stripe 2); and spraying or pasting the second coding stripe 16 near any one of the first coding stripe 2, the second coding stripe 16 has only one white stripe (that is, the white stripe is positioned at the first black and white stripe Near the coding stripe 2, and there is only one white stripe), the white stripe of the second coding stripe 16 is used as a key phase signal.
[0038] Facing each coded stripe (i.e. a group of...
Embodiment 2
[0045] Combine below Figure 1 to Figure 4 The scheme in Example 1 is discussed in detail, see the following description for details:
[0046] The embodiment of the present invention adopts fiber optic timing sensor 3, see figure 2 , has the advantages of lightness, softness, and good electromagnetic compatibility, and is suitable for on-site applications. Some on-site environments require a large working distance of the probe (that is, the distance from the end face of the probe to the axis) for safety reasons, and a focusing and collimating structure is designed.
[0047]The fiber optic timing sensor 3 adopts Y-shaped fiber bundle, and the central fiber is the transmitting fiber, which closely surrounds M receiving fibers, which can be precisely circled 1 or 2 times. Generally, M=6 is sufficient to meet the requirements.
[0048] The laser light source 10 transmits and emits the laser light through the emitting fiber, and collimates and emits the laser light through the f...
PUM
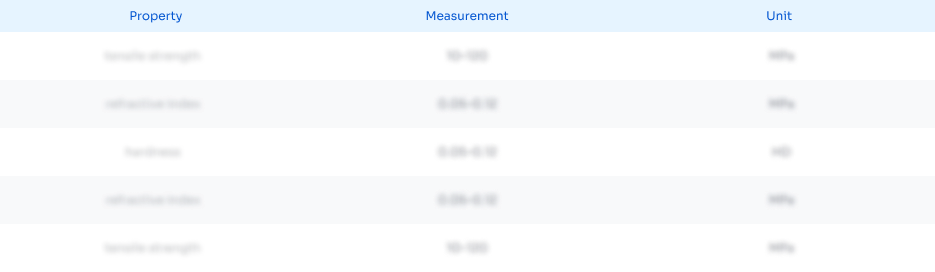
Abstract
Description
Claims
Application Information

- R&D
- Intellectual Property
- Life Sciences
- Materials
- Tech Scout
- Unparalleled Data Quality
- Higher Quality Content
- 60% Fewer Hallucinations
Browse by: Latest US Patents, China's latest patents, Technical Efficacy Thesaurus, Application Domain, Technology Topic, Popular Technical Reports.
© 2025 PatSnap. All rights reserved.Legal|Privacy policy|Modern Slavery Act Transparency Statement|Sitemap|About US| Contact US: help@patsnap.com