Methods of making thermoplastic fiber composites and webs
A technology of fiber materials and composite materials, applied in the field of manufacturing composites including thermoplastic particles and lignocellulosic fibers, to achieve uniform filler distribution, improve dehydration, and reduce costs
- Summary
- Abstract
- Description
- Claims
- Application Information
AI Technical Summary
Problems solved by technology
Method used
Image
Examples
Embodiment Construction
[0045] Definition of Precipitated Calcium Carbonate (PCC)
[0046] Almost all PCC is made by the direct carbonation of slaked lime, known as milk of lime. Slaking lime with water to form Ca(OH) 2 , and to precipitate calcium carbonate (insoluble in water), slaked lime is combined with (captured) carbon dioxide. PCC can then be used in the paper industry as filler or pigment, mineral or coated mineral or in plastic or barrier layers. It can also be used as a filler in plastics or as an additive in household care products, toothpaste, food, pharmaceuticals, paints, inks, etc.
[0047] Definition of Online Precipitated Calcium Carbonate Process
[0048] "On-line production" means producing precipitated calcium carbonate (PCC) directly in the papermaking raw material stream, i.e. combining captured carbon dioxide with slaked lime milk in-line, rather than producing PCC separately from the papermaking process. The separate production of PCC further requires the use of reten...
PUM
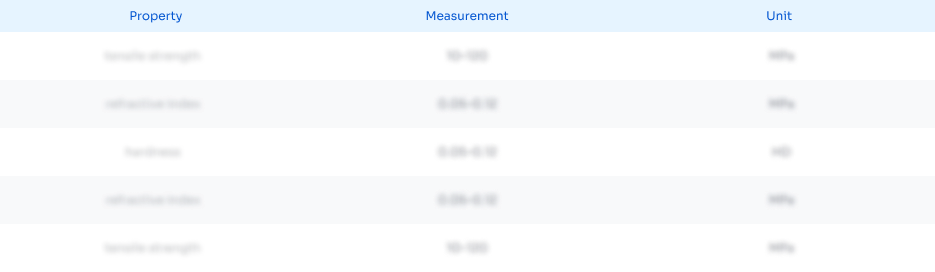
Abstract
Description
Claims
Application Information

- R&D Engineer
- R&D Manager
- IP Professional
- Industry Leading Data Capabilities
- Powerful AI technology
- Patent DNA Extraction
Browse by: Latest US Patents, China's latest patents, Technical Efficacy Thesaurus, Application Domain, Technology Topic, Popular Technical Reports.
© 2024 PatSnap. All rights reserved.Legal|Privacy policy|Modern Slavery Act Transparency Statement|Sitemap|About US| Contact US: help@patsnap.com