A rear end structure of a hybrid electric bus
A hybrid, tail-end technology, applied in the superstructure, superstructure sub-assemblies, vehicle components, etc., can solve the problems of low safety, poor strength, poor versatility, etc., and achieve high safety performance, light overall weight, and versatility. strong effect
- Summary
- Abstract
- Description
- Claims
- Application Information
AI Technical Summary
Problems solved by technology
Method used
Image
Examples
Embodiment Construction
[0060] The present invention will be further described below in conjunction with accompanying drawing:
[0061] Such as Figure 1-Figure 4 The rear end structure of a hybrid electric bus shown includes a hybrid nine-piece beam 2, an engine compartment frame assembly 3 installed above the hybrid nine-piece beam 2, and symmetrically arranged on the left and right sides of the middle section of the hybrid nine-piece beam 2 The engine left tail longitudinal beam assembly 4 and the engine right tail longitudinal beam assembly 5, the cooling module mounting bracket 8 arranged on the left side of the engine left tail longitudinal beam assembly 4, and the cooling module installation bracket 8 arranged on the right side of the engine right tail longitudinal beam assembly 5 Several post-processing system mounting brackets, the first connecting bracket 7 connecting the engine compartment frame assembly 3 and the cooling module mounting bracket 8, and the second connecting bracket 7 used ...
PUM
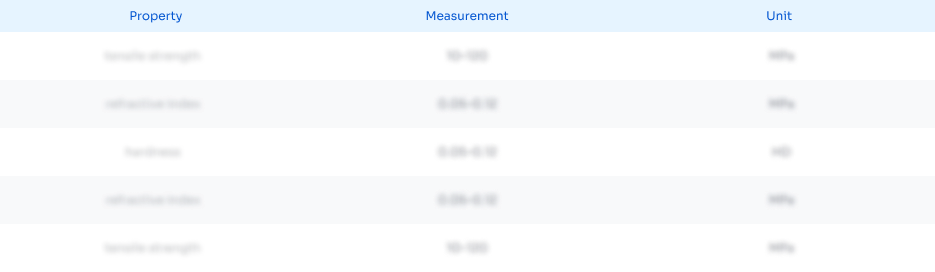
Abstract
Description
Claims
Application Information

- R&D
- Intellectual Property
- Life Sciences
- Materials
- Tech Scout
- Unparalleled Data Quality
- Higher Quality Content
- 60% Fewer Hallucinations
Browse by: Latest US Patents, China's latest patents, Technical Efficacy Thesaurus, Application Domain, Technology Topic, Popular Technical Reports.
© 2025 PatSnap. All rights reserved.Legal|Privacy policy|Modern Slavery Act Transparency Statement|Sitemap|About US| Contact US: help@patsnap.com