A Communication System for CAN Bus Precise Timing and Pipeline Testing
A CAN bus, communication system technology, applied in the field of communication systems, to achieve the effects of improving communication reliability, ensuring reliable transmission, and facilitating problem location
- Summary
- Abstract
- Description
- Claims
- Application Information
AI Technical Summary
Problems solved by technology
Method used
Image
Examples
Embodiment Construction
[0048] Below in conjunction with accompanying drawing and embodiment a kind of that the present invention provides is introduced:
[0049]A CAN bus precise timing and pipeline test communication system, including actuator A1, actuator B2, actuator C3, driver A4, driver B6, driver C10, ground control power supply module A5, with CAN bus communication Interface card 8, CAN bus timing communication system 7, ground power supply module B9 and CAN bus, wherein ground power supply module B9 is connected to actuator A1, actuator B2, and actuator C3 respectively, and ground control power supply module A5 They are respectively connected to driver A4, driver B6 and driver C10, the CAN bus is connected to driver A4, driver B6 and driver C10 respectively, actuator A1 is connected to driver C10, actuator B2 is connected to driver B6, and actuator C3 is connected to driver A4 is connected, with a CAN bus communication interface card 8 set on the CAN bus timing communication system 7, with a...
PUM
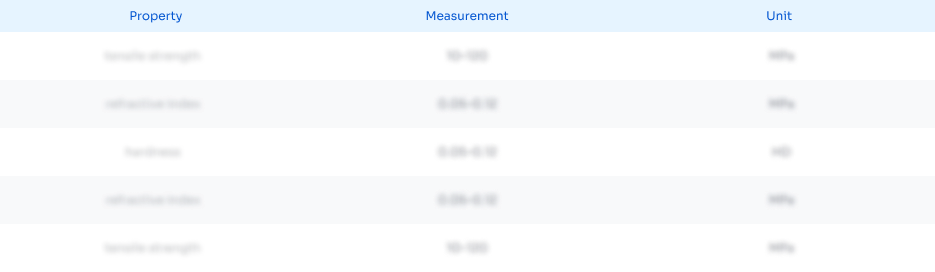
Abstract
Description
Claims
Application Information

- Generate Ideas
- Intellectual Property
- Life Sciences
- Materials
- Tech Scout
- Unparalleled Data Quality
- Higher Quality Content
- 60% Fewer Hallucinations
Browse by: Latest US Patents, China's latest patents, Technical Efficacy Thesaurus, Application Domain, Technology Topic, Popular Technical Reports.
© 2025 PatSnap. All rights reserved.Legal|Privacy policy|Modern Slavery Act Transparency Statement|Sitemap|About US| Contact US: help@patsnap.com