Combined sprue basin
A sprue basin and combined technology, which is applied in the direction of casting molding equipment, metal processing equipment, and mold composition, can solve the problems of reducing the ratio of sand to iron and the amount of sand eaten by the mold, and achieve the goal of reducing the amount of sand used Effect
- Summary
- Abstract
- Description
- Claims
- Application Information
AI Technical Summary
Problems solved by technology
Method used
Image
Examples
Embodiment Construction
[0025] Embodiments of the present invention will be described in detail with reference to the drawings.
[0026] refer to figure 1 , the present invention provides a combined sprue basin, the combined sprue basin is used to pour molten iron into the mold, and it is characterized in that it includes: a sprue basin 10; a sprue seat 2, and the sprue seat 2 is nested in the sprue basin 10, and between the sprue basin 10 and the upper box of the mold (not shown). The combined sprue basin of the present invention uses the sprue seat 2 between the sprue basin 10 and the mold to avoid the problem of increasing the amount of sand eaten by the mold in the prior art in order to ensure the height of the remaining pressure head, that is, the cast The mold increases the height of the remaining pressure head without increasing the amount of sand consumed, reduces the amount of sand used in the mold, and reduces the waste of resources and costs.
[0027] refer to Figure 2-3 The sprue basi...
PUM
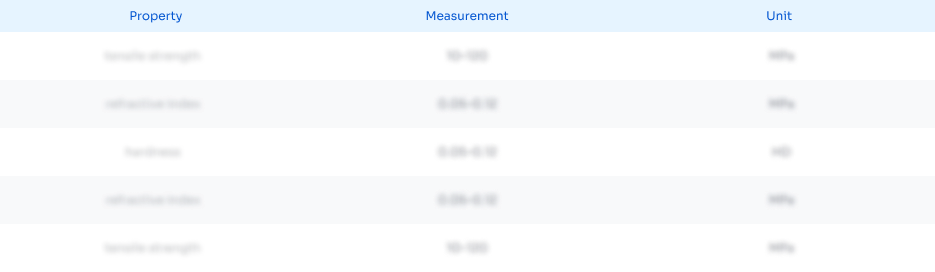
Abstract
Description
Claims
Application Information

- R&D
- Intellectual Property
- Life Sciences
- Materials
- Tech Scout
- Unparalleled Data Quality
- Higher Quality Content
- 60% Fewer Hallucinations
Browse by: Latest US Patents, China's latest patents, Technical Efficacy Thesaurus, Application Domain, Technology Topic, Popular Technical Reports.
© 2025 PatSnap. All rights reserved.Legal|Privacy policy|Modern Slavery Act Transparency Statement|Sitemap|About US| Contact US: help@patsnap.com