Endoscope cutting stapler
A stapler and endoscopic technology, applied in the field of medical devices, can solve the problems of large operating force, narrow operating space, large triangular-alveolar meshing area, etc.
- Summary
- Abstract
- Description
- Claims
- Application Information
AI Technical Summary
Problems solved by technology
Method used
Image
Examples
Embodiment Construction
[0036] The present invention is described below in conjunction with accompanying drawing.
[0037] At present, the known laparoscopic cutting stapler is used in surgical operations, and the stapler includes a butt-mounted execution assembly 100, a jaw direction adjustment mechanism 200, and a stapler driving part 300; the execution assembly 100 includes at least an upper jaw with a molded groove Mouth 102, lower jaw 101 with staple cartridge, joint connecting plate 105, elastic push plate 104 and component sleeve 107; stapler driving part 300 at least includes shell and operable handle 301; jaw direction adjustment mechanism 200 is set The front end of the stapler driving part 300 is connected by a connecting rib 272 .
[0038] as attached Figure 1-9 As shown, in the first embodiment of the present invention, the jaw direction adjustment mechanism 200 includes a joint knob 260, a main turntable 110, a shrapnel assembly 120, a slave turntable 130, a ring gear 150, a transmiss...
PUM
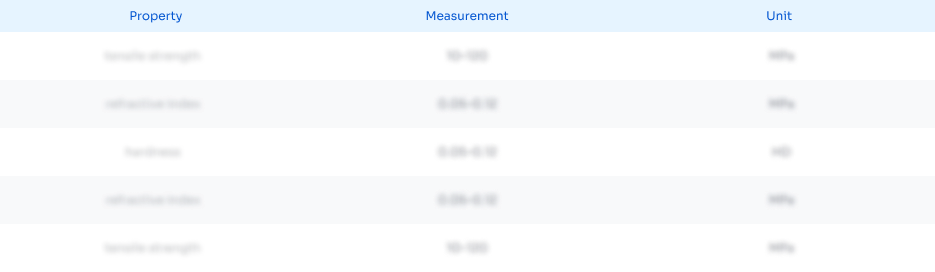
Abstract
Description
Claims
Application Information

- Generate Ideas
- Intellectual Property
- Life Sciences
- Materials
- Tech Scout
- Unparalleled Data Quality
- Higher Quality Content
- 60% Fewer Hallucinations
Browse by: Latest US Patents, China's latest patents, Technical Efficacy Thesaurus, Application Domain, Technology Topic, Popular Technical Reports.
© 2025 PatSnap. All rights reserved.Legal|Privacy policy|Modern Slavery Act Transparency Statement|Sitemap|About US| Contact US: help@patsnap.com