Modeling and optimization method for piston compressor vibration isolation system
A technology of vibration isolation system and optimization method, applied in the field of compressors, can solve problems such as poor vibration reduction effect, inability to effectively support the system, easy to jump, etc., and achieve the effect of improving precision and accuracy
- Summary
- Abstract
- Description
- Claims
- Application Information
AI Technical Summary
Problems solved by technology
Method used
Image
Examples
Embodiment Construction
[0026] Embodiments of the present invention will be further described below in conjunction with the accompanying drawings. This embodiment is carried out on the premise of the technical solution of the present invention, and detailed implementation and specific operation process are given, but the protection scope of the present invention is not limited to the following embodiments. This embodiment is only an explanation of the present invention, and those skilled in the art can make modifications without creative contribution to this embodiment as required after reading this specification, but they are all protected by the patent law within the scope of the claims of the present invention.
[0027] The modeling and optimization method of the piston compressor vibration isolation system of the present invention comprises the following steps:
[0028] 1. The rigid body dynamics model of the piston compressor is simplified, and the rigid body dynamics model of the piston compres...
PUM
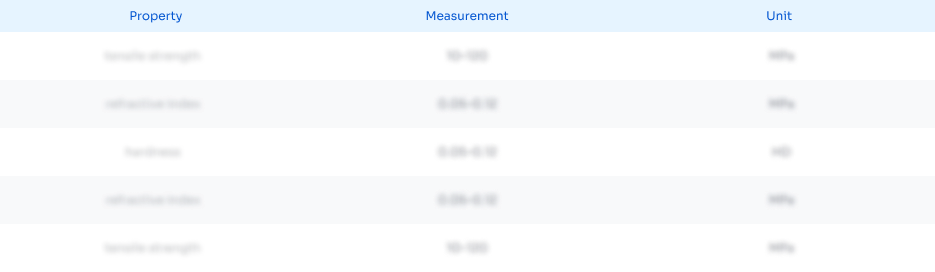
Abstract
Description
Claims
Application Information

- R&D
- Intellectual Property
- Life Sciences
- Materials
- Tech Scout
- Unparalleled Data Quality
- Higher Quality Content
- 60% Fewer Hallucinations
Browse by: Latest US Patents, China's latest patents, Technical Efficacy Thesaurus, Application Domain, Technology Topic, Popular Technical Reports.
© 2025 PatSnap. All rights reserved.Legal|Privacy policy|Modern Slavery Act Transparency Statement|Sitemap|About US| Contact US: help@patsnap.com