A Multidisciplinary Reliability Modeling Method for Hydraulic Servo Mechanism Based on Fault Mechanism
A failure mechanism, hydraulic servo technology, applied in the direction of electrical digital data processing, special data processing applications, instruments, etc.
- Summary
- Abstract
- Description
- Claims
- Application Information
AI Technical Summary
Problems solved by technology
Method used
Image
Examples
Embodiment Construction
[0079] The present invention is a multidisciplinary reliability modeling method of hydraulic servo mechanism based on failure mechanism, such as figure 1 Shown; The method is carried out according to the following five stages successively; The present invention adopts the connecting rod mechanism controlled by hydraulic pressure as a case, and the specific implementation is described in detail as follows:
[0080] Phase 1: System Modeling
[0081] System modeling is divided into the following three steps:
[0082] Step ⑴ Dynamic Mechanism Modeling:
[0083] In ADAMS, the 3D solid model of the connecting rod mechanism with the nominal size of the mechanism is first established. The solid model is shown in Figure 2; after that, constraints and kinematic pairs are added to the 3D model. The kinematic pair numbers in the ADAMS model are as follows: image 3 shown. Among them, the housing of the connecting rod mechanism is fixedly connected to the ground; the front and rear slid...
PUM
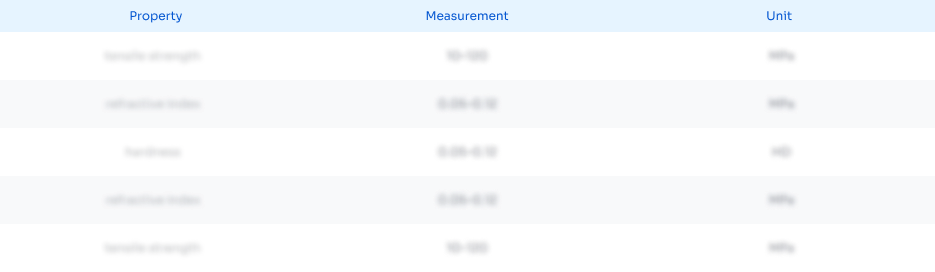
Abstract
Description
Claims
Application Information

- R&D
- Intellectual Property
- Life Sciences
- Materials
- Tech Scout
- Unparalleled Data Quality
- Higher Quality Content
- 60% Fewer Hallucinations
Browse by: Latest US Patents, China's latest patents, Technical Efficacy Thesaurus, Application Domain, Technology Topic, Popular Technical Reports.
© 2025 PatSnap. All rights reserved.Legal|Privacy policy|Modern Slavery Act Transparency Statement|Sitemap|About US| Contact US: help@patsnap.com