Operation method for electric vehicle carriage welding assembly line
A welding assembly line and electric vehicle technology, applied in the direction of welding equipment, welding equipment, auxiliary welding equipment, etc., can solve the problems of reducing the labor intensity of employees, achieve the effect of reducing the labor intensity of employees, reducing labor intensity, and solving the difference in working hours
- Summary
- Abstract
- Description
- Claims
- Application Information
AI Technical Summary
Problems solved by technology
Method used
Image
Examples
Embodiment 1
[0017] The first temporary storage frame 2 is set between the first lifting frame 1 and the second lifting frame 3, the second temporary storage frame 4 is set between the second lifting frame 3 and the third lifting frame 5, and the third lifting frame A self-turning frame 12 is arranged at the end of the frame 5; the structures of the first lifting frame 1, the second lifting frame 3 and the third lifting frame 5 are the same, all of which are: a lifting mechanism 7 is set in the mobile frame 6, and the lifting mechanism Support platform 9 is arranged above 7, and cylinder 8 is arranged between the base of lifting mechanism 7 and support platform 9, and at least two rows of horn bearings 10 are evenly distributed along the direction of operation process above support platform 9; The structures of the storage racks 4 are the same, both: a temporary storage platform 11 is set above the mobile frame 6, and at least two rows of horn bearings 10 are evenly distributed above the te...
Embodiment 2
[0019] The first lifting frame 1, the first temporary storage frame 2, the second lifting frame 3, the second temporary storage frame 4, and the third lifting frame 5 are connected in turn to form the whole welding line, and move from the turning frame 12 to the third lifting frame. Behind the lifting frame 5, the carriage substrate is placed above the horn bearing 10 of the support platform 9 of the first lifting frame 1, and the carriage substrate is finely adjusted and slid above the horn bearing 10 to the position to be processed, and each component is welded on the carriage substrate, and the welding After completion, the cylinder 8 in the lifting mechanism 7 of the first lifting frame 1 promotes the support platform 9 to rise, so that the support platform 9 and the temporary storage platform 11 of the first temporary storage frame 2 are located on the same horizontal line, and the carriage substrate is pushed along the horn bearing. 10 slides to the top of the horn bearin...
PUM
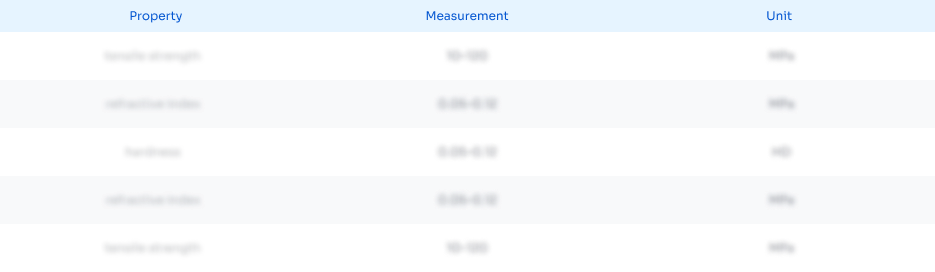
Abstract
Description
Claims
Application Information

- R&D Engineer
- R&D Manager
- IP Professional
- Industry Leading Data Capabilities
- Powerful AI technology
- Patent DNA Extraction
Browse by: Latest US Patents, China's latest patents, Technical Efficacy Thesaurus, Application Domain, Technology Topic, Popular Technical Reports.
© 2024 PatSnap. All rights reserved.Legal|Privacy policy|Modern Slavery Act Transparency Statement|Sitemap|About US| Contact US: help@patsnap.com