A grinding wheel automatic production line
An automatic production line and grinding wheel technology, applied in metal processing equipment, grinding devices, grinding/polishing equipment, etc., can solve the problems of low work efficiency, time-consuming and laborious manual leveling, cumbersome operation, etc., to achieve a balance between production efficiency and cost, The effect of improving molding quality and high feeding efficiency
- Summary
- Abstract
- Description
- Claims
- Application Information
AI Technical Summary
Problems solved by technology
Method used
Image
Examples
Embodiment Construction
[0050] The present invention will be further described below in conjunction with the accompanying drawings.
[0051] figure 1 As shown, an automatic grinding wheel production line includes a production track 1, a grinding wheel forming mold 2, a mesh placement system 3, a feeding system 4, a feeding system 5, a scraping system 6, a pressing system 7, a core ring placement system 8, a molding Machine 9, film pulling system 10. The grinding wheel forming mold 2 is slidingly set on the production track 1, and the production track 1 is sequentially equipped with a mesh placement system 3, a feeding system 4, a feeding system 5, a scraping system 6, a mesh placement system, a pressing system 7, a core The ring placement system 8 and the molding press 9, the molding press 9 is provided with a film drawing system 10 corresponding to the grinding wheel forming mold 2 on the production track 1.
[0052] Figure 2-6 As shown, the mesh placement system 3 includes a mesh support frame ...
PUM
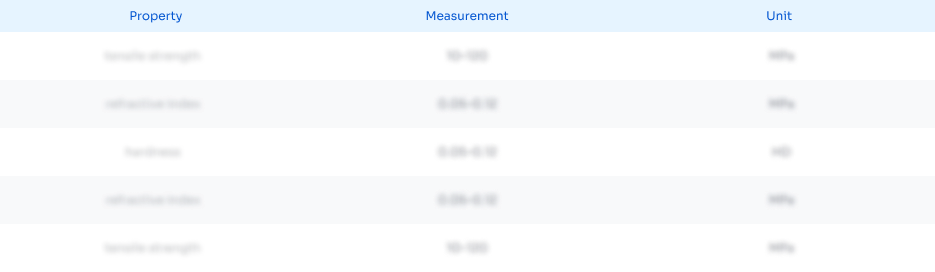
Abstract
Description
Claims
Application Information

- R&D
- Intellectual Property
- Life Sciences
- Materials
- Tech Scout
- Unparalleled Data Quality
- Higher Quality Content
- 60% Fewer Hallucinations
Browse by: Latest US Patents, China's latest patents, Technical Efficacy Thesaurus, Application Domain, Technology Topic, Popular Technical Reports.
© 2025 PatSnap. All rights reserved.Legal|Privacy policy|Modern Slavery Act Transparency Statement|Sitemap|About US| Contact US: help@patsnap.com