Self-driven rotation shaft vibration and local position stabilization system
A technology for stabilizing system and space vibration stabilization, applied in the direction of using feedback control, etc., can solve the problems of no explanation or report, large driving torque, complex structure, etc., to reduce the degree of filling density or stress transmission, and strengthen vibration isolation. Effects, compact effects
- Summary
- Abstract
- Description
- Claims
- Application Information
AI Technical Summary
Problems solved by technology
Method used
Image
Examples
Embodiment Construction
[0090] The present invention will be described in detail below in conjunction with specific embodiments. The following examples will help those skilled in the art to further understand the present invention, but do not limit the present invention in any form. It should be noted that those skilled in the art can make several changes and improvements without departing from the concept of the present invention. These all belong to the protection scope of the present invention.
[0091] According to the vibration and local position stabilization system of a self-driven rotating shaft provided by the present invention, such as Figure 14 , Figure 15 As shown, it includes a space vibration stabilization device; the space vibration stabilization device includes: a load plate, a drive electromagnetic device, a transfer entity, a permanent magnet isolation plate, and a transfer housing; the transfer entity matched with the transfer housing is arranged on the load For the disk, the ...
PUM
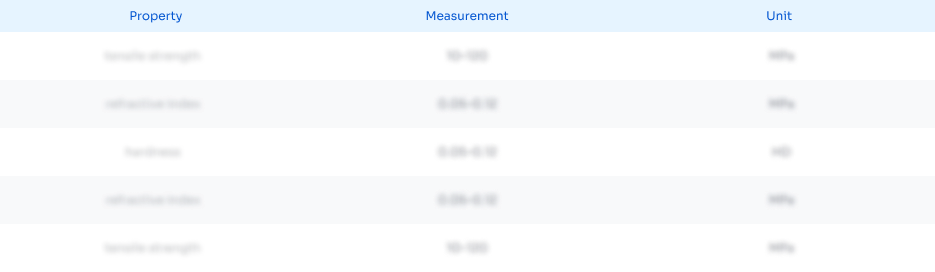
Abstract
Description
Claims
Application Information

- R&D Engineer
- R&D Manager
- IP Professional
- Industry Leading Data Capabilities
- Powerful AI technology
- Patent DNA Extraction
Browse by: Latest US Patents, China's latest patents, Technical Efficacy Thesaurus, Application Domain, Technology Topic, Popular Technical Reports.
© 2024 PatSnap. All rights reserved.Legal|Privacy policy|Modern Slavery Act Transparency Statement|Sitemap|About US| Contact US: help@patsnap.com