High-strength reinforced concrete pipe culvert and preparation method thereof
A reinforced concrete, high-strength technology, which is applied in the field of concrete box culverts, can solve the problems that the index of crack load and failure load is difficult to reach the standard, and the quality of high-strength reinforced concrete box culverts is poor.
- Summary
- Abstract
- Description
- Claims
- Application Information
AI Technical Summary
Problems solved by technology
Method used
Examples
preparation example Construction
[0014] The invention provides a method for preparing a high-strength reinforced concrete box culvert, comprising:
[0015] 1) Soak the calcined shells in the activation solution, then filter, dry and sieve to obtain the calcined shells;
[0016] 2) Mixing cement, calcined shells, stones, sand, fly ash and water to prepare concrete;
[0017] 3) Concrete is poured into the reinforced skeleton, and then cured to obtain a high-strength reinforced concrete box culvert;
[0018] Wherein, the activation solution contains water, hydrochloric acid, sulfurous acid and dimercaptopropanol.
[0019] In the activation solution of the present invention, the amount of each component can be selected within a wide range, but in order to enable the activation solution to further activate the calcined shells, preferably, in step 1), relative to 100 parts by weight of water , the consumption of hydrochloric acid is 15-20 parts by weight, the consumption of sulfurous acid is 7-11 parts by weight,...
Embodiment 1
[0029] 1) Soak the calcined shells in the activation solution at 80°C for 16 hours (the weight ratio of the calcined shells to the activation solution is 100:400), then filter, dry at 135°C until the moisture content is lower than 1%, and pass through 200 mesh The activated shell calcined product is prepared by sieving; wherein, the activation solution contains water, hydrochloric acid, sulfurous acid and dimercapto propanol (weight ratio is 100:17:8:4).
[0030] 2) Mix cement, calcined shells, stones, sand, fly ash and water (weight ratio: 100:30:180:200:60:270) to make concrete.
[0031] 3) Concrete was poured into the steel frame, and then cured for 4 days under the conditions of -3°C and 55% relative humidity to prepare a high-strength reinforced concrete box culvert A1.
Embodiment 2
[0033] 1) Soak the calcined shells in the activation solution at 70°C for 12 hours (the weight ratio of the calcined shells to the activation solution is 100:300), then filter, dry at 120°C until the moisture content is lower than 1%, pass through 200 mesh The activated shell calcined product is prepared by sieving; wherein, the activation solution contains water, hydrochloric acid, sulfurous acid and dimercapto propanol (weight ratio is 100:15:7:3).
[0034] 2) Mix cement, calcined activated shells, stones, sand, fly ash and water (weight ratio: 100:20:150:180:50:250) to prepare concrete.
[0035] 3) Concrete was poured into the steel skeleton, and then cured for 3 days under the conditions of -5°C and 50% relative humidity to prepare a high-strength reinforced concrete box culvert A2.
PUM
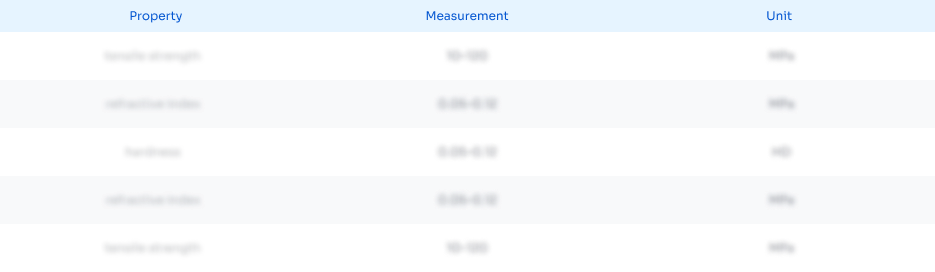
Abstract
Description
Claims
Application Information

- R&D Engineer
- R&D Manager
- IP Professional
- Industry Leading Data Capabilities
- Powerful AI technology
- Patent DNA Extraction
Browse by: Latest US Patents, China's latest patents, Technical Efficacy Thesaurus, Application Domain, Technology Topic, Popular Technical Reports.
© 2024 PatSnap. All rights reserved.Legal|Privacy policy|Modern Slavery Act Transparency Statement|Sitemap|About US| Contact US: help@patsnap.com