Gravity-driven reciprocating mechanism
A reciprocating mechanism, gravity-driven technology, applied in mechanical equipment, transmission elements, transmission devices, etc., can solve problems such as unstable driving load capacity, insufficient motor voltage compensation, and insufficient motor torque enhancement.
- Summary
- Abstract
- Description
- Claims
- Application Information
AI Technical Summary
Problems solved by technology
Method used
Image
Examples
Embodiment Construction
[0040] The present invention will now be further described in detail in conjunction with the accompanying drawings and embodiments. These drawings are all simplified schematic diagrams, only illustrating the basic structure of the present invention in a schematic manner, so it only shows the composition related to the present invention.
[0041] Such as figure 1 with figure 2 As shown, a reciprocating mechanism driven by gravity includes: a driving mechanism and a toggle mechanism connected by a fork lever 8, the driving mechanism includes a driving gear 3 that can mesh with the first gear 1 and the second gear 2 respectively, and the driving gear 3 Slidingly arranged on the drive shaft 4, the first gear 1 and the second gear 2 rotate in opposite directions; the toggle mechanism includes a slidingly arranged shift lever 7, and two shift fork levers 8 are arranged on the shift lever 7, and the two shift fork levers 8 are respectively Located at the outer sides of both ends of...
PUM
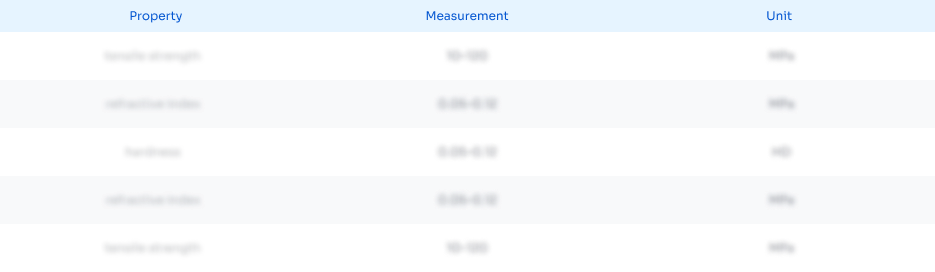
Abstract
Description
Claims
Application Information

- R&D Engineer
- R&D Manager
- IP Professional
- Industry Leading Data Capabilities
- Powerful AI technology
- Patent DNA Extraction
Browse by: Latest US Patents, China's latest patents, Technical Efficacy Thesaurus, Application Domain, Technology Topic, Popular Technical Reports.
© 2024 PatSnap. All rights reserved.Legal|Privacy policy|Modern Slavery Act Transparency Statement|Sitemap|About US| Contact US: help@patsnap.com