Automatic up-and-down device of line patrol robot of strain tower
A technology of line inspection robots and tension rods, applied in cranes, transportation and packaging, overhead lines/cable equipment, etc., can solve problems such as low work efficiency, potential safety hazards, and high labor intensity
- Summary
- Abstract
- Description
- Claims
- Application Information
AI Technical Summary
Problems solved by technology
Method used
Image
Examples
Embodiment Construction
[0026] The technical solutions of the present invention will be further specifically described below through the embodiments and in conjunction with the accompanying drawings.
[0027] Examples of the automatic on-line and off-line device of the tension pole tower line inspection robot of the present invention figure 1 As shown, the foundation pile 6 is a pole tower spliced by angle steel, which is fixed on the ground at a certain distance from the tension pole tower head 10; The ends are the stay wire 4 and the guide wire 3 respectively; the stay wire 4 is drawn from the side of the winch 2 close to the foundation pile 6, guided upward by a number of fixed pulleys 5 installed on the foundation pile, and then passed through the tower head installed on the tower head of the tension pole. The bridge crossing device is connected to the ground wire of the tension pole tower.
[0028] The fixed pulley 5 is fixed on the foundation pile 6 at a certain distance through the support ...
PUM
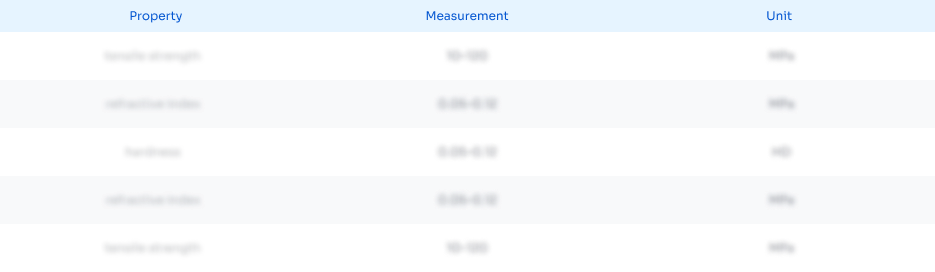
Abstract
Description
Claims
Application Information

- R&D Engineer
- R&D Manager
- IP Professional
- Industry Leading Data Capabilities
- Powerful AI technology
- Patent DNA Extraction
Browse by: Latest US Patents, China's latest patents, Technical Efficacy Thesaurus, Application Domain, Technology Topic, Popular Technical Reports.
© 2024 PatSnap. All rights reserved.Legal|Privacy policy|Modern Slavery Act Transparency Statement|Sitemap|About US| Contact US: help@patsnap.com