Vibration locus tracking control method for two-dimensional ultrasonically-assisted grinding
An ultrasonic-assisted, vibrating trajectory technology used in grinding automatic control devices, grinding machine parts, grinding/polishing equipment, etc.
- Summary
- Abstract
- Description
- Claims
- Application Information
AI Technical Summary
Problems solved by technology
Method used
Image
Examples
Embodiment Construction
[0035] In order to obtain the same vibration effect of the ultrasonic elliptical vibration at each processing point in the ultrasonic assisted machining, the present invention realizes a tracking control algorithm that keeps the relative posture and shape unchanged between the ultrasonic elliptical vibration trajectory and the normal direction of the workpiece. Make the ultrasonic elliptical vibration trajectory follow the processing trajectory. When the grinding wheel moves to each processing point on the processing trajectory, according to the needs of optical aspheric processing control, the ultrasonic elliptical vibration trajectory is always kept perpendicular to the normal direction of the current processing point on the workpiece surface. And the shape of the relative vibration track remains unchanged, so that the processing effect with consistent surface distribution can be obtained. The auxiliary control method controls the input electrical signal of the two-phase powe...
PUM
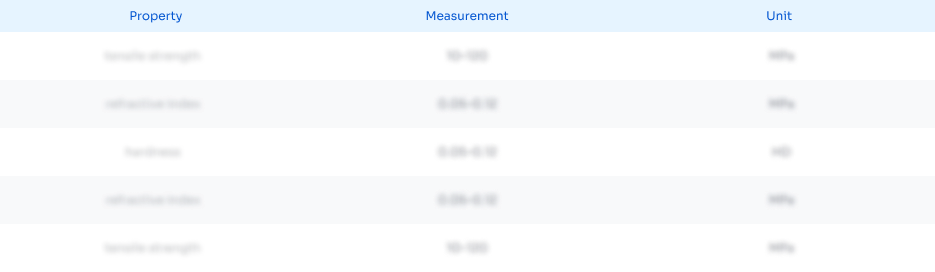
Abstract
Description
Claims
Application Information

- Generate Ideas
- Intellectual Property
- Life Sciences
- Materials
- Tech Scout
- Unparalleled Data Quality
- Higher Quality Content
- 60% Fewer Hallucinations
Browse by: Latest US Patents, China's latest patents, Technical Efficacy Thesaurus, Application Domain, Technology Topic, Popular Technical Reports.
© 2025 PatSnap. All rights reserved.Legal|Privacy policy|Modern Slavery Act Transparency Statement|Sitemap|About US| Contact US: help@patsnap.com