Anti-pilling cellulosic fiber knitted fabric and production method of same
A technology of cellulose fiber and production method, which is applied in knitting, weft knitting, fabric surface trimming, etc., can solve the problems of cellulose fiber easy to pilling, etc., and achieve high elastic extensibility, soft and comfortable hand feeling, and small elastic recovery force Effect
- Summary
- Abstract
- Description
- Claims
- Application Information
AI Technical Summary
Problems solved by technology
Method used
Examples
Embodiment 1
[0013] A kind of anti-pilling cellulose fiber knitted fabric and its production method, using the blended yarn of cellulose fiber and cotton fiber and spandex screw as raw materials, through the steps of spinning, weaving and presetting, the specific steps are as follows:
[0014] The first step, spun yarn: the drawing process is introduced in the spun yarn processing stage, and the two fiber strips composed of cellulose fiber strips and cotton are mixed and drafted to obtain a blended yarn of cellulose fibers and cotton fibers;
[0015] The second step, weaving: use the blended yarn of cellulose fiber and cotton fiber as the ground yarn and spandex screw, and use the weft flat needle shovel weaving method to weave. Each weaving system uses a ground yarn and a spandex bare wire Plating yarns are woven together to obtain a weft-knitted single-sided plain needle plating fabric;
[0016] The third step, pre-setting: After the fabric is woven, it is heated and pre-shaped, and the ...
Embodiment 2
[0023] A kind of anti-pilling cellulose fiber knitted fabric and its production method, using the blended yarn of cellulose fiber and cotton fiber and spandex screw as raw materials, through the steps of spinning, weaving and presetting, the specific steps are as follows:
[0024] The first step, spun yarn: the drawing process is introduced in the spun yarn processing stage, and the two fiber strips composed of cellulose fiber strips and cotton are mixed and drafted to obtain a blended yarn of cellulose fibers and cotton fibers;
[0025] The second step, weaving: use the blended yarn of cellulose fiber and cotton fiber as the ground yarn and spandex screw, and use the weft flat needle shovel weaving method to weave. Each weaving system uses a ground yarn and a spandex bare wire Plating yarns are woven together to obtain a weft-knitted single-sided plain needle plating fabric;
[0026] The third step, pre-setting: After the fabric is woven, it is heated and pre-shaped, and the ...
Embodiment 3
[0033] A kind of anti-pilling cellulose fiber knitted fabric and its production method, using the blended yarn of cellulose fiber and cotton fiber and spandex screw as raw materials, through the steps of spinning, weaving and presetting, the specific steps are as follows:
[0034] The first step, spun yarn: the drawing process is introduced in the spun yarn processing stage, and the two fiber strips composed of cellulose fiber strips and cotton are mixed and drafted to obtain a blended yarn of cellulose fibers and cotton fibers;
[0035] The second step, weaving: use the blended yarn of cellulose fiber and cotton fiber as the ground yarn and spandex screw, and use the weft flat needle shovel weaving method to weave. Each weaving system uses a ground yarn and a spandex bare wire Plating yarns are woven together to obtain a weft-knitted single-sided plain needle plating fabric;
[0036] The third step, pre-setting: After the fabric is woven, it is heated and pre-shaped, and the ...
PUM
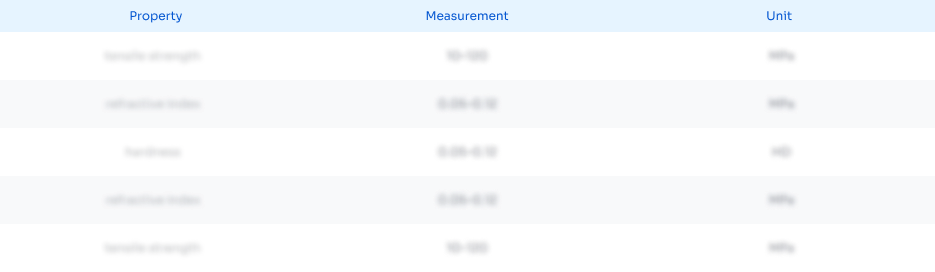
Abstract
Description
Claims
Application Information

- R&D Engineer
- R&D Manager
- IP Professional
- Industry Leading Data Capabilities
- Powerful AI technology
- Patent DNA Extraction
Browse by: Latest US Patents, China's latest patents, Technical Efficacy Thesaurus, Application Domain, Technology Topic, Popular Technical Reports.
© 2024 PatSnap. All rights reserved.Legal|Privacy policy|Modern Slavery Act Transparency Statement|Sitemap|About US| Contact US: help@patsnap.com