Method for real-time estimation of tool abrasion condition of cutter head tunneling system of hard rock tunnel boring machine
A technology for tunneling and tool wear, which is applied in tunnels, earthwork drilling, instruments, etc., can solve the problems that cannot effectively reflect the real-time prediction of tool wear in the hard rock TBM cutter head tunneling system in real time, so as to improve tunneling efficiency and optimize Effect of tunneling parameters
- Summary
- Abstract
- Description
- Claims
- Application Information
AI Technical Summary
Problems solved by technology
Method used
Image
Examples
Embodiment 1
[0045] In the tunnel engineering of this embodiment, the structural parameters of the hard rock TBM used are as follows: cutterhead radius R=2.885m, 42 17in disc-shaped hobs are installed on the cutterhead, and the cutter installation radius on each cutter station is shown above figure 1 shown in the example described. The project is constructed under mixed granite geological conditions, and the detailed steps for estimating the wear and replacement of TBM cutterhead tools are given as follows:
[0046] The first step is to determine the change law of the energy consumption of the cutterhead tunneling system in the direction of cutterhead rotation with the energy consumption of the tunneling direction during the tunneling process of hard rock TBM:
[0047] The energy in the rotation direction of the hard rock TBM cutter head tunneling system has the following theoretical relationship with the energy in the tunneling direction:
[0048] E. r '=a·E p 0.67324 (1)
[0049]...
PUM
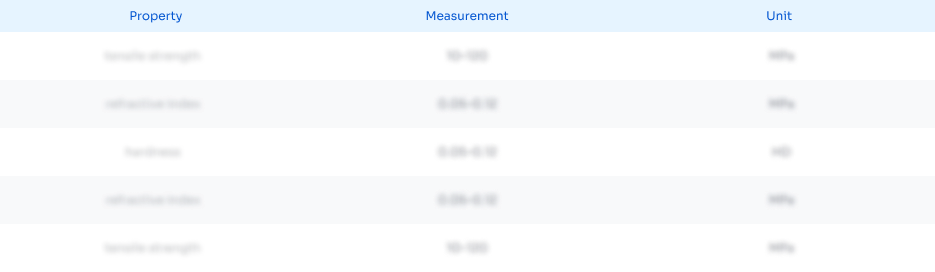
Abstract
Description
Claims
Application Information

- R&D
- Intellectual Property
- Life Sciences
- Materials
- Tech Scout
- Unparalleled Data Quality
- Higher Quality Content
- 60% Fewer Hallucinations
Browse by: Latest US Patents, China's latest patents, Technical Efficacy Thesaurus, Application Domain, Technology Topic, Popular Technical Reports.
© 2025 PatSnap. All rights reserved.Legal|Privacy policy|Modern Slavery Act Transparency Statement|Sitemap|About US| Contact US: help@patsnap.com