A shearing damping tube and vibration damping adapter with vibration damping performance
A technology of shearing and damping tubes, applied in the direction of non-rotational vibration suppression, etc., can solve problems such as poor vibration damping effect, achieve good stiffness, good vibration damping performance, and improve the effect of mechanical environment
- Summary
- Abstract
- Description
- Claims
- Application Information
AI Technical Summary
Problems solved by technology
Method used
Image
Examples
Embodiment 1
[0027] see Figure 1-6 , a shear type damping tube with vibration damping performance, comprising an aluminum alloy joint 1, a carbon fiber tube 2, a damping rubber layer 3, an aluminum alloy casing 4, and a steel spring tube 5, the upper section of the carbon fiber tube 2 and the The aluminum alloy joint 1 is bonded and connected, the outer side of the lower section of the carbon fiber tube 2 is connected to the inner side of the aluminum alloy casing 4 through the damping glue layer 3, and the inner side of the lower section of the carbon fiber tube 2 is connected to the steel spring The outer side of the tube 5 is adhesively connected, and the aluminum alloy casing 4 is connected to the steel spring tube 5 .
[0028] see image 3 , the aluminum alloy joint 1 includes a sleeve 12 and an ear piece 11, the ear piece 11 is connected to the top of the sleeve 12, and the outer side of the sleeve 12 is connected to the upper section of the carbon fiber tube 2 through an adhesive ...
Embodiment 2
[0034] The present invention also provides a vibration-damping adapter, which includes the shear-type damping tube with vibration-damping performance of Embodiment 1. The following is a preferred embodiment.
[0035] The damping adapter consists of an upper end frame, eight upper end frame joints, sixteen above-mentioned shear damping tubes, and eight lower end joints. The eight upper and lower end joints are distributed symmetrically in the circumferential direction, and each joint is connected to two damping tubes. tubes, each damping tube is cross-connected with the upper and lower joints. The upper end frame is fixedly connected with the launch vehicle, and the lower end joint is fixedly connected with the satellite. The vibration-damping adapter not only has good vibration-damping performance, but also has a good rigidity index, and can improve the mechanical environment of the satellite payload in the active flight section of the rocket.
PUM
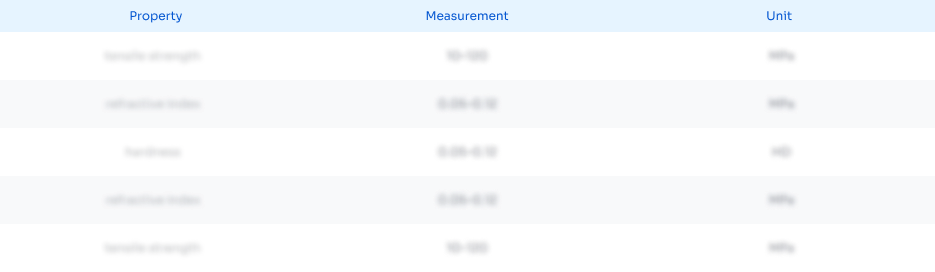
Abstract
Description
Claims
Application Information

- R&D
- Intellectual Property
- Life Sciences
- Materials
- Tech Scout
- Unparalleled Data Quality
- Higher Quality Content
- 60% Fewer Hallucinations
Browse by: Latest US Patents, China's latest patents, Technical Efficacy Thesaurus, Application Domain, Technology Topic, Popular Technical Reports.
© 2025 PatSnap. All rights reserved.Legal|Privacy policy|Modern Slavery Act Transparency Statement|Sitemap|About US| Contact US: help@patsnap.com