All-hydraulic autonomous moving manipulator and moving method thereof
An autonomous moving, robotic arm technology, applied in the field of robotic arms, can solve the problems of workers' occupational health hazards, high labor intensity, serious vulcanization pollution, etc., achieve the improvement of workers' occupational health level, huge market value, and meet the needs of large-scale mobile operations. Effect
- Summary
- Abstract
- Description
- Claims
- Application Information
AI Technical Summary
Problems solved by technology
Method used
Image
Examples
Embodiment Construction
[0041] In order to make the technical problems, technical solutions and advantages to be solved by the present invention clearer, the following will describe in detail with reference to the drawings and specific embodiments.
[0042] On the one hand, the present invention provides a kind of fully hydraulic self-moving manipulator, such as Figure 1 to Figure 2 As shown, the omnidirectional mobile platform 1 is included, and the omnidirectional mobile platform 1 is provided with a double robot arm 2, a power system, a visual system, and a perception and control system, wherein:
[0043]The omnidirectional mobile platform 1 is provided with a rotating waist device 11, and the double mechanical arm 2 is arranged on the omnidirectional mobile platform 1 through the rotating waist device 11. The double robotic arm 2 is a humanoid double arm structure with multiple degrees of freedom;
[0044] The power system adopts engine-hydraulic drive mode;
[0045] The visual system includes ...
PUM
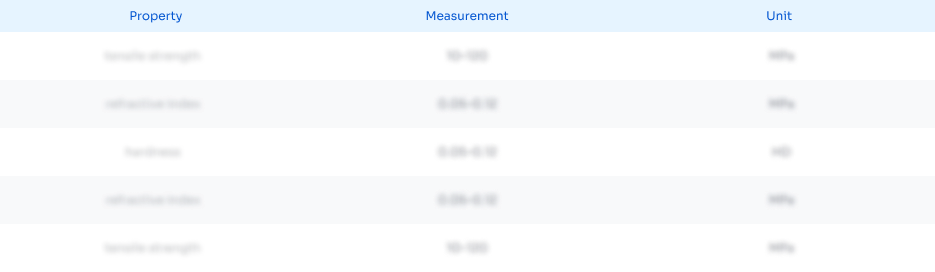
Abstract
Description
Claims
Application Information

- R&D
- Intellectual Property
- Life Sciences
- Materials
- Tech Scout
- Unparalleled Data Quality
- Higher Quality Content
- 60% Fewer Hallucinations
Browse by: Latest US Patents, China's latest patents, Technical Efficacy Thesaurus, Application Domain, Technology Topic, Popular Technical Reports.
© 2025 PatSnap. All rights reserved.Legal|Privacy policy|Modern Slavery Act Transparency Statement|Sitemap|About US| Contact US: help@patsnap.com