Oversized ferrite for particle acceleration device and preparation method of oversized ferrite
A super-sized, particle-accelerated technology, applied in the field of materials, can solve problems such as high production costs, limited performance, and deformation
- Summary
- Abstract
- Description
- Claims
- Application Information
AI Technical Summary
Problems solved by technology
Method used
Image
Examples
Embodiment 1
[0038] Each component is weighed according to the following mass percentage: 55.9% Fe 2 o 3 , 18% NiO, 16% ZnO, 3.5% CuO, 1.8% Co 2 o 3 , 1.3% MnCO 3 , 0.5% V 2 o 5 , 3.0% magnesium chloride hexahydrate.
[0039]After mixing the weighed components, water was added thereto, and then the obtained mixture was ball-milled for 15 hours to obtain a ball-milled product. The prepared primary ball milling product was then dried, and after drying, the first ball milling product was pre-calcined at a pre-calcination temperature of 1060° C. and a pre-calcination time of 3 hours to obtain a pre-calcined product. After the calcined product is cooled, water is added to the pre-calcined product, and then ball milled for a second time. The time of the second ball milling is 4 hours to obtain a second ball milled product. After the secondary ball milling product is dried, the secondary ball milling product is pressed and molded to obtain a molded product, and the molding pressure is 2.5*...
Embodiment 2
[0041] Each component is weighed according to the following mass percentage: 59.1% Fe 2 o 3 , 15% NiO, 15% ZnO, 2% CuO, 2.0% Co 2 o 3 , 1.6% MnCO 3 , 0.8% V 2 o 5 , 4.5% magnesium chloride hexahydrate.
[0042] After mixing the weighed components, water was added thereto, and then the obtained mixture was ball-milled for 20 hours to obtain a ball-milled product. The prepared primary ball mill product is then dried, and after drying, the first ball mill product is pre-calcined at a pre-calcination temperature of 1080° C. to 1090° C. and a pre-calcination time of 5 hours to obtain a pre-calcined product. After the calcined product is cooled, water is added to the calcined product, and ball milling is carried out for a second time. The second ball milling time is 6 hours to obtain a second ball milled product. After the secondary ball milling product is dried, the secondary ball milling product is pressed and molded to obtain a molding, and the molding pressure is 2.3*10 ...
Embodiment 3
[0044] Each component is weighed according to the following mass percentage: 54.1% Fe 2 o 3 , 15% NiO, 18% ZnO, 3% CuO, 2.0% Co 2 o 3 , 1.6% MnCO 3 , 0.8% V 2 o 5 , 5.5% magnesium chloride hexahydrate.
[0045] After mixing the weighed components, deionized pure water was added thereto, and then the obtained mixture was ball-milled for 12 hours to obtain a ball-milled product. The prepared primary ball milling product was then dried, and after drying, the first ball milling product was pre-calcined at a pre-calcination temperature of 1070° C. and a pre-calcination time of 4 hours to obtain a pre-calcined product. After the pre-calcined product is cooled, water is added to the pre-calcined product, and a second ball milling is carried out, and the time of the second ball milling is 3-7 hours to obtain a second ball milled product. After the secondary ball milling product is dried, the secondary ball milling product is pressed and molded to obtain a molding, and the moldi...
PUM
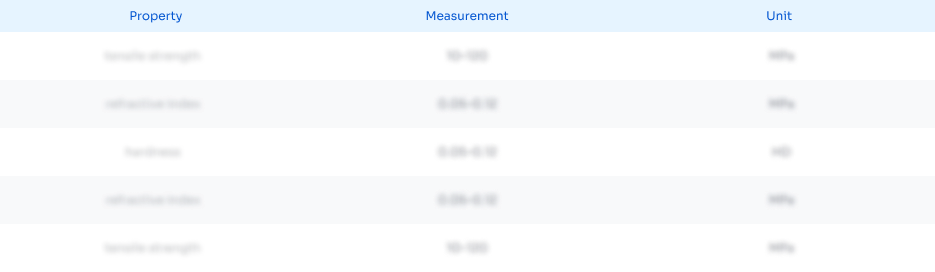
Abstract
Description
Claims
Application Information

- R&D Engineer
- R&D Manager
- IP Professional
- Industry Leading Data Capabilities
- Powerful AI technology
- Patent DNA Extraction
Browse by: Latest US Patents, China's latest patents, Technical Efficacy Thesaurus, Application Domain, Technology Topic, Popular Technical Reports.
© 2024 PatSnap. All rights reserved.Legal|Privacy policy|Modern Slavery Act Transparency Statement|Sitemap|About US| Contact US: help@patsnap.com