Electric control separation mechanism of unmanned aerial vehicle and parachute
A separation mechanism and parachute technology, applied in the directions of parachutes, aircraft parts, transportation and packaging, can solve the problems of unsafe explosive storage, damage and collision of drones or airborne equipment, and achieve simple and practical structural principles and large applications. The effect of strong value and carrying capacity
- Summary
- Abstract
- Description
- Claims
- Application Information
AI Technical Summary
Problems solved by technology
Method used
Image
Examples
Embodiment Construction
[0014] The present invention will be further described below in conjunction with the accompanying drawings and embodiments. While the invention will be described in conjunction with the preferred embodiments, it will be understood that it is not intended to limit the invention to the described embodiments. On the contrary, the invention is to cover alternatives, modifications and equivalents, which may be included within the scope of the invention as defined by the appended claims.
[0015] refer to Figure 1 to Figure 2 As shown, the electronically controlled separation mechanism for the UAV and the parachute in this embodiment consists of three parts: a rotary device, an electromagnet and a locking device. The slewing device adopts the ball-pin slewing pair structure, which is composed of slewing ball head 1, pin shaft 2 and slewing sleeve 3. The head and the end cover 4 are connected in the form of a rotary pair, and the end cover 4 is fixedly connected with the frame 6 t...
PUM
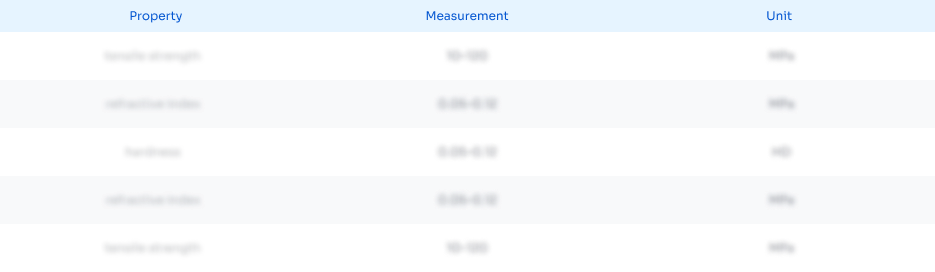
Abstract
Description
Claims
Application Information

- R&D
- Intellectual Property
- Life Sciences
- Materials
- Tech Scout
- Unparalleled Data Quality
- Higher Quality Content
- 60% Fewer Hallucinations
Browse by: Latest US Patents, China's latest patents, Technical Efficacy Thesaurus, Application Domain, Technology Topic, Popular Technical Reports.
© 2025 PatSnap. All rights reserved.Legal|Privacy policy|Modern Slavery Act Transparency Statement|Sitemap|About US| Contact US: help@patsnap.com