Method for designing linearity of mounting surface for rolling linear guide of precision machine tool
A linear guide rail and precision machine tool technology, applied in computing, special data processing applications, instruments, etc., can solve problems such as demanding parts accuracy, and achieve the effect of shortening the product development cycle
- Summary
- Abstract
- Description
- Claims
- Application Information
AI Technical Summary
Problems solved by technology
Method used
Image
Examples
Embodiment Construction
[0025] Such as figure 1 As shown, the design method of the straightness tolerance of the rolling linear guide rail mounting surface of the precision machine tool of the present invention comprises the following steps:
[0026] 1) Since it is more complicated to obtain the modal basis function by the analytical method, the system can be discretized, and the modal vector can be obtained conveniently by using the finite element software, and then the normalization principle ||Y can be used i || ∞ =1, the uniquely determined modal basis function is obtained. According to the size of the guide rail, the modal basis function Y of the assembly characteristic surface is obtained by using ANSYS finite element software;
[0027] The shape error of the guide rail is expressed by the modal basis function and the modal coefficient, and the mean value of the modal coefficient μ of the guide rail is obtained by using the mapping relationship between the shape error of the guide rail and th...
PUM
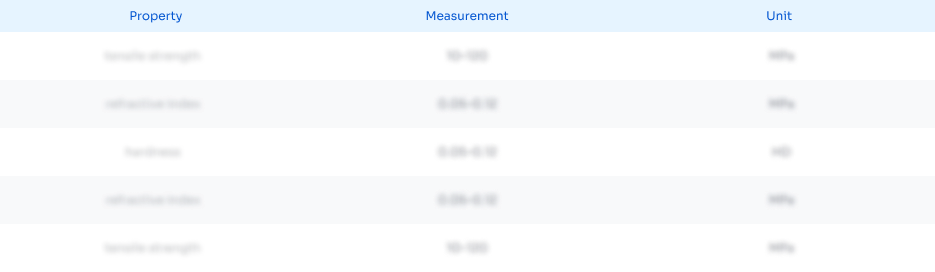
Abstract
Description
Claims
Application Information

- R&D
- Intellectual Property
- Life Sciences
- Materials
- Tech Scout
- Unparalleled Data Quality
- Higher Quality Content
- 60% Fewer Hallucinations
Browse by: Latest US Patents, China's latest patents, Technical Efficacy Thesaurus, Application Domain, Technology Topic, Popular Technical Reports.
© 2025 PatSnap. All rights reserved.Legal|Privacy policy|Modern Slavery Act Transparency Statement|Sitemap|About US| Contact US: help@patsnap.com