Control method of combined positioning control system
A control system and combined positioning technology, which is applied in the direction of conveyor control devices, conveyor objects, transportation and packaging, etc., can solve the problems of high precision and low cost, and achieve the effect of high positioning precision, high cost performance and no cumulative error
- Summary
- Abstract
- Description
- Claims
- Application Information
AI Technical Summary
Problems solved by technology
Method used
Image
Examples
Embodiment 1
[0064] This embodiment 1 introduces a combined positioning control system and control method for carrying a trolley 2 on a workpiece processing production line.
[0065] Figure 4 Among them, the carrying trolley 2 needs to carry the workpiece 10 to a specific station of the processing production line for the manipulator on the station to pick up, and the positioning accuracy is ±0.1mm, Figure 4 Only two positioning positions are drawn, so two laser reflectors 7 are required.
[0066] Such as figure 1 , Figure 4 Among them, the positioning structure of this embodiment includes a screw rod 1, a carrying trolley 2, a motor reducer 3, a multi-turn absolute value encoder 4, a laser ranging sensor 5, a fixed workbench 6, a laser reflector 7, and a trolley running guide rail 8 and a fixed base plate 9; the electrical control system includes a touch screen, a processor, an industrial control computer, a CAN bus communication card and a motor driver; the fixed workbench 6 and the...
PUM
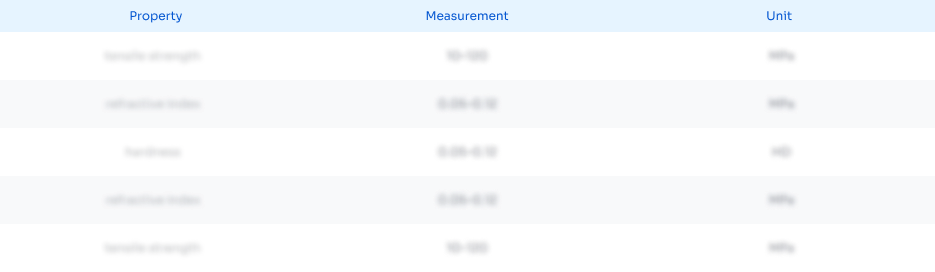
Abstract
Description
Claims
Application Information

- Generate Ideas
- Intellectual Property
- Life Sciences
- Materials
- Tech Scout
- Unparalleled Data Quality
- Higher Quality Content
- 60% Fewer Hallucinations
Browse by: Latest US Patents, China's latest patents, Technical Efficacy Thesaurus, Application Domain, Technology Topic, Popular Technical Reports.
© 2025 PatSnap. All rights reserved.Legal|Privacy policy|Modern Slavery Act Transparency Statement|Sitemap|About US| Contact US: help@patsnap.com