Improvements in gasification and/or pyrolysis
A technology of pyrolysis and hot gas, which is applied in the field of gasification and pyrolysis of waste), which can solve the problems of clogging and reducing the effectiveness of stirring devices.
- Summary
- Abstract
- Description
- Claims
- Application Information
AI Technical Summary
Problems solved by technology
Method used
Image
Examples
Embodiment Construction
[0023] As mentioned above, the invention can be used in gasification / pyrolysis chambers described in prior art documents as static or as rotating. The embodiments specifically described herein relate to a rotating version of the chamber, although it will be apparent to those skilled in the art how the invention can be modified for use with a static version of the oven. The protection scope of the present invention is not limited to the above two forms (static form and rotating form).
[0024] figure 1 with figure 2 Shown is a gasification / pyrolysis machine having a housing 2 in which a process chamber 1 is mounted to contain and process material. The material may be waste material comprising organic components, such as municipal waste or industrial waste, or alternatively any material comprising organic matter. The waste is loaded into a removable container 4 which is then connected to the device.
[0025] The hot air enters the processing chamber 1 through the intake pip...
PUM
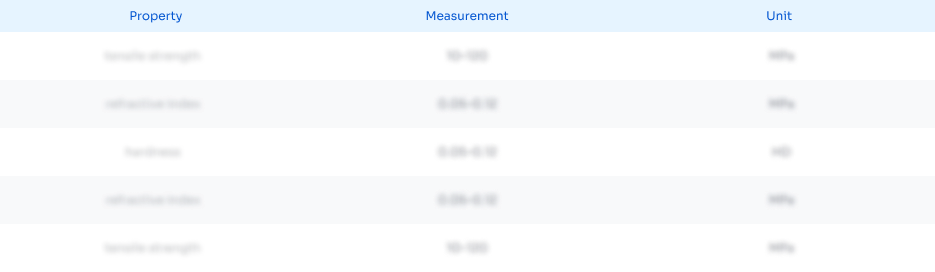
Abstract
Description
Claims
Application Information

- R&D Engineer
- R&D Manager
- IP Professional
- Industry Leading Data Capabilities
- Powerful AI technology
- Patent DNA Extraction
Browse by: Latest US Patents, China's latest patents, Technical Efficacy Thesaurus, Application Domain, Technology Topic, Popular Technical Reports.
© 2024 PatSnap. All rights reserved.Legal|Privacy policy|Modern Slavery Act Transparency Statement|Sitemap|About US| Contact US: help@patsnap.com