Production method and forge die of high-speed train brake disc
A technology for high-speed trains and brake discs, applied in the field of forging processing, can solve the problems of low production efficiency and few presses, and achieve the effects of improving production efficiency, avoiding defects, and avoiding shrinkage and deformation.
- Summary
- Abstract
- Description
- Claims
- Application Information
AI Technical Summary
Benefits of technology
Problems solved by technology
Method used
Image
Examples
Embodiment Construction
[0020] Below in conjunction with accompanying drawing and specific embodiment, further illustrate the present invention, should be understood that these embodiments are only for illustrating the present invention and are not intended to limit the scope of the present invention, after having read the present invention, those skilled in the art will understand various aspects of the present invention Modifications in equivalent forms all fall within the scope defined by the appended claims of this application.
[0021] Such as figure 1 As shown in ~ 4, the high-speed train brake disc of the present invention is in the shape of a ring disc, and a plurality of cooling ribs are evenly distributed on its upper surface. In order to solve the problem that the top corners of the cooling ribs are full during forging, a special forging die is used. The forging die includes an upper die and a lower die. cavity, which corresponds to the structure of the brake disc; the bottom of the lower...
PUM
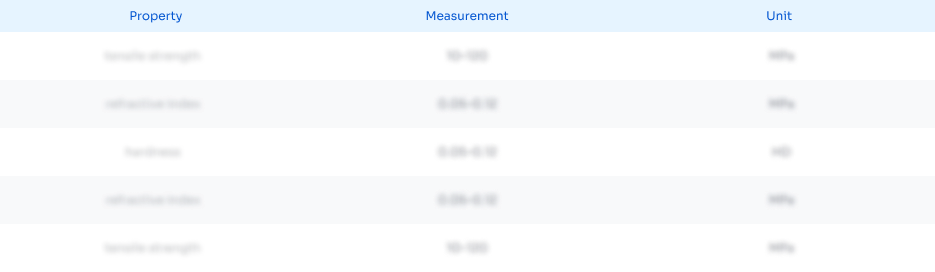
Abstract
Description
Claims
Application Information

- Generate Ideas
- Intellectual Property
- Life Sciences
- Materials
- Tech Scout
- Unparalleled Data Quality
- Higher Quality Content
- 60% Fewer Hallucinations
Browse by: Latest US Patents, China's latest patents, Technical Efficacy Thesaurus, Application Domain, Technology Topic, Popular Technical Reports.
© 2025 PatSnap. All rights reserved.Legal|Privacy policy|Modern Slavery Act Transparency Statement|Sitemap|About US| Contact US: help@patsnap.com