A Prediction Method of Rolling Mill Torsional Vibration
A prediction method and rolling mill technology, applied in the direction of rolling mill control devices, metal rolling, metal rolling, etc., can solve the problems of high-quality and high-precision strip steel products, the inability to adjust the prediction model in real time, and the difficulty in establishing prediction parameter equations, etc. to avoid different subjective judgment standards, increase objective evaluation standards, and simplify the torsional vibration prediction process
- Summary
- Abstract
- Description
- Claims
- Application Information
AI Technical Summary
Problems solved by technology
Method used
Image
Examples
Embodiment Construction
[0025] The present invention is described in detail below in conjunction with accompanying drawing:
[0026] 1. See figure 1 A torsional vibration experiment platform is built with AC variable frequency motor, reducer, work roll at the load end, torsional vibration sensor, elastic connection shaft, speed sensor and host computer. Through the serial port in the host computer, the speed sensor transmits the rolling speed of the rolling mill to On the upper computer, the torsional vibration sensor transmits the detected torsional vibration response in the elastic connecting shaft to the upper computer, and the rolling speed v is set to change between 20m / s and 100m / s, and the rolling precision p is between 10% and 0.1%. Change, the surface quality sq of the strip steel product changes between 0 and 9, the roll gap lubrication level rl changes between 0 and 9, take different combination values for v, p, sq, rl, denoted by c, c( n) represents the nth combined value.
[0027] 2....
PUM
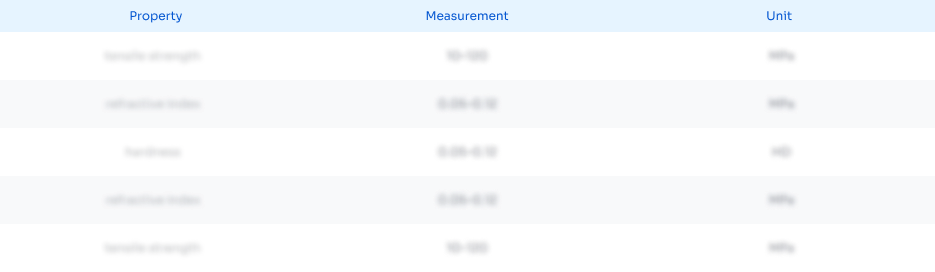
Abstract
Description
Claims
Application Information

- R&D
- Intellectual Property
- Life Sciences
- Materials
- Tech Scout
- Unparalleled Data Quality
- Higher Quality Content
- 60% Fewer Hallucinations
Browse by: Latest US Patents, China's latest patents, Technical Efficacy Thesaurus, Application Domain, Technology Topic, Popular Technical Reports.
© 2025 PatSnap. All rights reserved.Legal|Privacy policy|Modern Slavery Act Transparency Statement|Sitemap|About US| Contact US: help@patsnap.com