Laser tracking multi-station positioning method for super-large gears
A technology of laser tracking and positioning method, which is applied in the direction of using optical devices, measuring devices, instruments, etc., can solve the problems of insufficient precision, and achieve the effects of improving three-dimensional measurement accuracy, good precision control effect, and reliable data source
- Summary
- Abstract
- Description
- Claims
- Application Information
AI Technical Summary
Problems solved by technology
Method used
Image
Examples
Embodiment Construction
[0028] The present invention will be further described below in conjunction with accompanying drawing:
[0029] 1) if figure 1 As shown, several test points are arranged on the upper end face and addendum circle of the gear and numbered in sequence (the first test point, the second test point...the nth test point), usually according to the sequence of the test points. , the numbering sequence is not mandatory, but remember the numbers corresponding to each point to be measured and the total number n of points to be measured. Then move the reflector to each point to be measured according to the serial number of the point to be measured, and measure the three-dimensional coordinate value of the point to be measured on the gear. Move the laser tracker to different stations in turn. The station can be set at will, but make sure that the laser tracker can measure all the points to be measured at each station, and repeat the measurement of the points to be measured on the gear in t...
PUM
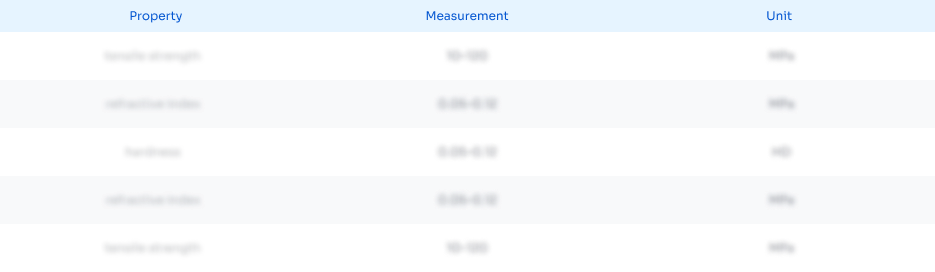
Abstract
Description
Claims
Application Information

- Generate Ideas
- Intellectual Property
- Life Sciences
- Materials
- Tech Scout
- Unparalleled Data Quality
- Higher Quality Content
- 60% Fewer Hallucinations
Browse by: Latest US Patents, China's latest patents, Technical Efficacy Thesaurus, Application Domain, Technology Topic, Popular Technical Reports.
© 2025 PatSnap. All rights reserved.Legal|Privacy policy|Modern Slavery Act Transparency Statement|Sitemap|About US| Contact US: help@patsnap.com