Full-aircraft beam frame type reduction stiffness combination modeling method
A modeling method and a full-machine technology, applied in special data processing applications, instruments, electrical digital data processing, etc., can solve problems such as difficult to accurately simulate the dynamic characteristics of complex structures, few degrees of freedom, huge units and degrees of freedom, etc. , to achieve the effect of convenient variable parameter analysis, convenient adjustment, and reduced calculation scale
- Summary
- Abstract
- Description
- Claims
- Application Information
AI Technical Summary
Problems solved by technology
Method used
Image
Examples
Embodiment
[0019] First, a reduced stiffness model is established. Select the finite element model of fuselage 1 and wing-body connection 2 as the research object, see figure 2 , set the reference point 3 at the centroid position of each frame section of the rod-plate finite element model, and use the RBE3 rigid body element 12 to reduce the corresponding section stiffness, the reduction form is as follows image 3 As shown, through the weighted average of nodes 4, 5, 6, 7, 8, 9, 10, and 11, the section stiffness is "condensed" to the reference point 3.
[0020] Secondly, output the stiffness matrix KAA corresponding to the reduced model through the DMAP statement. Since the stiffness matrix KAA does not contain reference point information, it is necessary to introduce the reference point information into the stiffness matrix KAA to generate the STIFF matrix.
[0021] Then, use the reference point, the STIFF matrix, and the quality characteristics corresponding to the rod-plate model t...
PUM
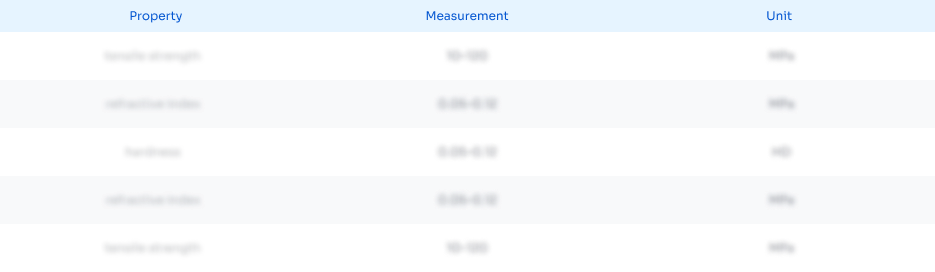
Abstract
Description
Claims
Application Information

- R&D
- Intellectual Property
- Life Sciences
- Materials
- Tech Scout
- Unparalleled Data Quality
- Higher Quality Content
- 60% Fewer Hallucinations
Browse by: Latest US Patents, China's latest patents, Technical Efficacy Thesaurus, Application Domain, Technology Topic, Popular Technical Reports.
© 2025 PatSnap. All rights reserved.Legal|Privacy policy|Modern Slavery Act Transparency Statement|Sitemap|About US| Contact US: help@patsnap.com