Roller screw rod with spacing bodies
A technology of roller screws and rollers, which is applied in the direction of belts/chains/gears, mechanical equipment, transmission devices, etc., and can solve problems such as increased distance between rollers, stuck roller screws, and reduced load capacity. Achieve the effects of shortening assembly time, saving processing costs, and easy assembly
- Summary
- Abstract
- Description
- Claims
- Application Information
AI Technical Summary
Problems solved by technology
Method used
Image
Examples
Embodiment Construction
[0063] In order to further explain the technical solution of the present invention, the present invention will be described in detail below through specific examples.
[0064] First of all, the spacer structure of the first preferred embodiment of the present invention is described, please refer to Figure 4A to Figure 4C As shown, it is a schematic diagram of the design process of the spacer of the present invention. There are two types of arrangement of the rollers in the existing common roller screw. One is: the axes of two adjacent rollers are arranged in the same direction, and the other is: The axes of two adjacent rollers are arranged in different directions, and the angle between the two axes is 90 degrees. This arrangement is as follows: Figure 4A shown. The structural design of the spacer 5 of the present invention comes from the arrangement of the axes of the two adjacent rollers in different directions. This is because the rollers arranged in different directions...
PUM
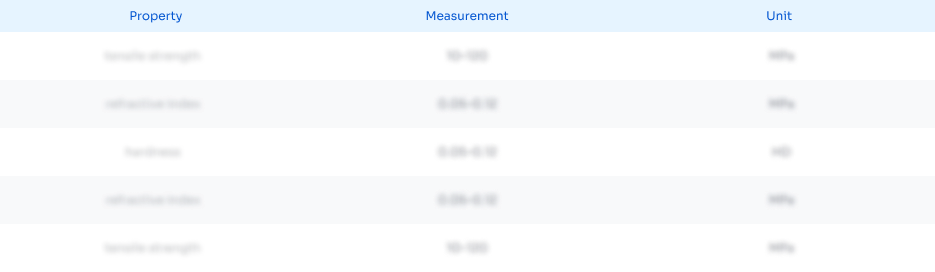
Abstract
Description
Claims
Application Information

- Generate Ideas
- Intellectual Property
- Life Sciences
- Materials
- Tech Scout
- Unparalleled Data Quality
- Higher Quality Content
- 60% Fewer Hallucinations
Browse by: Latest US Patents, China's latest patents, Technical Efficacy Thesaurus, Application Domain, Technology Topic, Popular Technical Reports.
© 2025 PatSnap. All rights reserved.Legal|Privacy policy|Modern Slavery Act Transparency Statement|Sitemap|About US| Contact US: help@patsnap.com